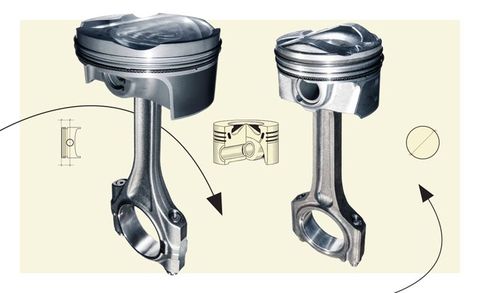
Die Aluminiumbutzen im Inneren Ihres Motors leben in einer feurigen Hölle. Bei Vollgas und 6000 Umdrehungen pro Minute ist ein Kolben in einem Benzinmotor alle 0,02 Sekunden einer Kraft von fast 10 Tonnen ausgesetzt, während wiederholte Explosionen das Metall auf über 600 Grad Celsius erhitzen.
Heute ist dieser zylindrische Hades heißer und intensiver denn je, und für die Kolben wird es wahrscheinlich nur noch schlimmer. Während die Autohersteller nach höherer Effizienz streben, bereiten sich die Kolbenhersteller auf eine Zukunft vor, in der die leistungsstärksten Benzin-Saugmotoren 175 PS pro Liter leisten, statt wie heute 130. Mit der Turboaufladung und der höheren Leistung kommen noch härtere Bedingungen. In den letzten zehn Jahren sind die Betriebstemperaturen der Kolben um 120 Grad gestiegen, während der Spitzendruck in den Zylindern von 1500 psi auf 2200 psi angewachsen ist.
Ein Kolben erzählt eine Geschichte über den Motor, in dem er sich befindet. Die Krone verrät die Bohrung, die Anzahl der Ventile und ob der Kraftstoff direkt in den Zylinder eingespritzt wird oder nicht. Doch das Design und die Technologie eines Kolbens können auch viel über die allgemeinen Trends und Herausforderungen in der Automobilindustrie aussagen. Um es mit einem Sprichwort zu sagen: Wie das Auto, so der Motor; und wie der Motor, so der Kolben. Auf der Suche nach einem geringeren Kraftstoffverbrauch und niedrigeren Emissionen verlangen die Automobilhersteller nach leichteren Kolben mit geringerer Reibung, die auch härteren Betriebsbedingungen standhalten können. Es sind diese drei Aspekte – Haltbarkeit, Reibung und Masse -, die den Arbeitstag der Kolbenlieferanten bestimmen.
In vielerlei Hinsicht folgt die Entwicklung der Ottomotoren dem Weg, den die Dieselmotoren vor 15 Jahren eingeschlagen haben. Um den um 50 Prozent höheren Spitzendruck in den Zylindern zu kompensieren, haben einige Aluminiumkolben jetzt einen Eisen- oder Stahleinsatz, um den oberen Ring zu stützen. Die heißesten Benzinmotoren werden bald einen Kühlkanal auf der Unterseite des Kolbenbodens benötigen, der die Wärme effizienter ableitet als die heutige Methode, die Unterseite des Kolbens einfach mit Öl zu besprühen. Die Sprühdüsen spritzen Öl in eine kleine Öffnung an der Unterseite des Kolbens, die den Kanal speist. Die scheinbar einfache Technologie ist jedoch nicht einfach herzustellen. Um einen Hohlraum zu schaffen, muss der Kolben in zwei Teile gegossen und durch Reibung oder Laserschweißen verbunden werden.
Kolben sind für mindestens 60 Prozent der Reibung im Motor verantwortlich, und Verbesserungen in diesem Bereich wirken sich direkt auf den Kraftstoffverbrauch aus. Reibungsmindernde, mit Graphit imprägnierte Harzflecken, die im Siebdruckverfahren auf die Schürze aufgebracht werden, sind inzwischen fast überall zu finden. Der Kolbenlieferant Federal-Mogul experimentiert mit einer verjüngten Fläche am Ölring, die eine Verringerung der Ringspannung ermöglicht, ohne den Ölverbrauch zu erhöhen. Eine geringere Ringreibung kann bis zu 0,15 PS pro Zylinder freisetzen.
Automobilhersteller sind auch auf der Suche nach neuen reibungsmindernden Oberflächen zwischen Teilen, die aneinander reiben oder sich drehen. Die harte und glatte diamantähnliche Beschichtung (DLC) ist vielversprechend für Zylinderlaufbuchsen, Kolbenringe und Kolbenbolzen, wo sie die Notwendigkeit von Lagern zwischen Bolzen und Pleuelstange beseitigen kann. Aber es ist teuer und hat nur wenige Anwendungen in den heutigen Autos.
„Es wird oft über DLC diskutiert, aber ob sie es in die Serienfahrzeuge schaffen, ist fraglich“, sagt Joachim Wagenblast, Senior Director of Product Development bei Mahle, einem deutschen Autozulieferer.
Immer ausgefeiltere Computermodelle und präzisere Fertigungsmethoden ermöglichen auch komplexere Formen. Zusätzlich zu den Mulden, Domen und Ventileinbuchtungen, die für das Spiel und das Erreichen eines bestimmten Verdichtungsverhältnisses erforderlich sind, weisen asymmetrische Kolbenschäfte einen kleineren, steiferen Bereich auf der Druckseite des Kolbens auf, um Reibung und Spannungskonzentrationen zu verringern. Wenn Sie einen Kolben umdrehen, sehen Sie konische Wände, die kaum mehr als 0,1 Zoll dick sind. Dünnere Wände erfordern eine engere Kontrolle der Toleranzen, die bereits in Mikrometern oder Tausendstel Millimetern gemessen werden.
Dünnere Wände erfordern auch ein besseres Verständnis der Wärmeausdehnung eines Objekts, das sich manchmal in Sekundenschnelle von unter dem Gefrierpunkt auf mehrere hundert Grad erwärmen muss. Das Metall in Ihrem Motor dehnt sich bei Erwärmung nicht gleichmäßig aus, so dass die Optimierung der Toleranzen die Erfahrung in der Konstruktion und die Fähigkeit zur präzisen Bearbeitung erfordert, um leichte Exzentrizitäten in den Teilen zu erzeugen.
„Nichts, was wir herstellen, ist absichtlich gerade oder rund“, sagt Keri Westbrooke, Direktorin für Konstruktion und Technologie bei Federal-Mogul. „Wir bauen immer einen gewissen Ausgleich ein.“
Kolben für Dieselmotoren durchlaufen ihre eigene Entwicklung, da der Spitzendruck in den Zylindern in Richtung 3600 psi steigt. Mahle und Federal-Mogul prognostizieren eine Verlagerung von gegossenen Aluminium- zu geschmiedeten Stahlkolben. Stahl ist dichter als Aluminium, aber dreimal stärker, was zu einem Kolben führt, der höheren Drücken und Temperaturen standhält, ohne an Gewicht zuzunehmen.
Stahl ermöglicht eine bemerkenswerte Änderung der Geometrie durch Verkürzung der Kompressionshöhe des Kolbens, definiert als der Abstand von der Mitte des Kolbenbolzens bis zum oberen Ende des Kolbenbodens. Dieser Bereich macht 80 Prozent des Kolbengewichts aus, weshalb kürzer in der Regel auch leichter bedeutet. Entscheidend ist, dass eine geringere Kompressionshöhe nicht nur die Kolben schrumpfen lässt. Sie ermöglicht auch einen kürzeren und leichteren Motorblock, da die Deckhöhe reduziert wird.
Mahle stellt Stahlkolben für modernste Turbodiesel-Anwendungen her, wie etwa für den vierfachen Le-Mans-Sieger Audi R18 TDI und den LMP2-Motor Skyactiv-D von Mazda. Noch in diesem Jahr wird das Unternehmen mit der Auslieferung seiner ersten Stahlkolben für einen leichten Seriendieselmotor, einen 1,5-Liter-Vierzylinder von Renault, beginnen.
Die anhaltende Bedeutung des Verbrennungsmotors ist auf die kontinuierliche Weiterentwicklung seiner Komponenten zurückzuführen. Kolben sind nicht sexy. Sie sind nicht so modisch wie eine Lithium-Ionen-Batterie, nicht so komplex wie ein Doppelkupplungsgetriebe und nicht so interessant wie ein drehmomentverteilendes Differential. Doch nach mehr als einem Jahrhundert des automobilen Fortschritts erzeugen Hubkolben nach wie vor den Großteil der Kraft, die uns bewegt.
Ferrari F136
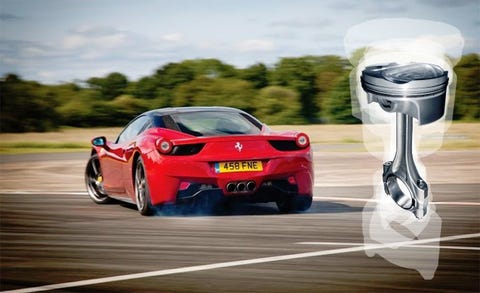
Applications: Ferrari 458 Italia (shown), 458 Spider
Engine Type: DOHC V-8
Displacement: 274 cu in, 4497 cc
Specific Output: 125.0 hp/l
Max engine speed: 9000 rpm
Bore: 3.70 in
Weight: 2.1 lb
Ford Fox
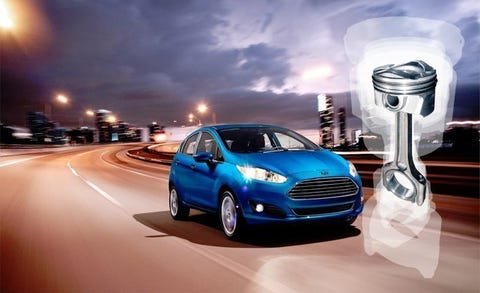
Applications: Ford Fiesta (shown), Focus
Engine Type: turbocharged DOHC inline-three
Displacement: 61 cu in, 999 cc
Specific Output: 123.1 hp/l
Max engine speed: 6500 rpm
Bore: 2.83 in
Weight: 1.5 lb
Cummins ISB 6.7

Applications: Ram Heavy Duty (shown)
Engine Type: turbocharged pushrod diesel inline-six
Displacement: 408 cu in, 6690 cc
Specific Output: 55.3 hp/l
Max engine speed: 3200 rpm
Bore: 4.21 in
Weight: 8.9 lb
Ford Coyote

Applications: Ford F-150, Mustang (shown)
Engine Type: DOHC V-8
Displacement: 302 cu in, 4951 cc
Specific Output: up to 84.8 hp/l
Max engine speed: 7000 rpm
Bore: 3.63 in
Weight: 2.4 lb
Fiat Fire 1.4L Turbo
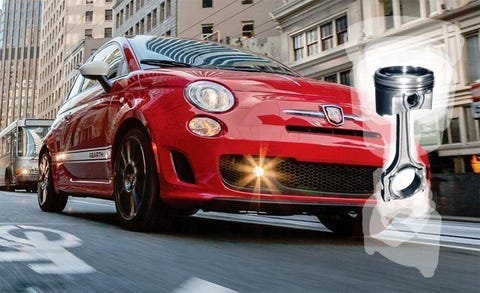
Applications: Dodge Dart; Fiat 500 Abarth (shown), 500L, 500 Turbo
Engine Type: turbocharged SOHC inline-four
Displacement: 83 cu in, 1368 cc
Specific Output: up to 117.0 hp/l
Max engine speed: 6500 rpm
Bore: 2.83 in
Weight: 1.5 lb
Cummins ISX15
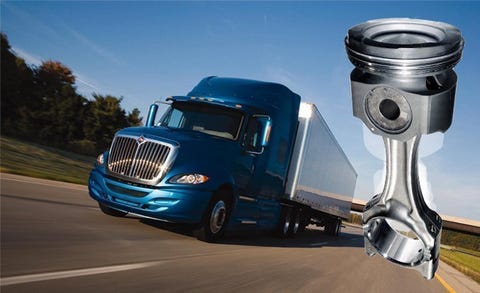
Applications: heavy-duty trucks (International Prostar shown)
Engine Type: turbocharged SOHC diesel inline-six
Displacement: 912 cu in, 14,948 cc
Specific Output: up to 40.1 hp/l
Max engine speed: 2000 rpm
Bore: 5.39 in
Weight: 26.4 lb
Chrysler LA-Series Magnum V-10
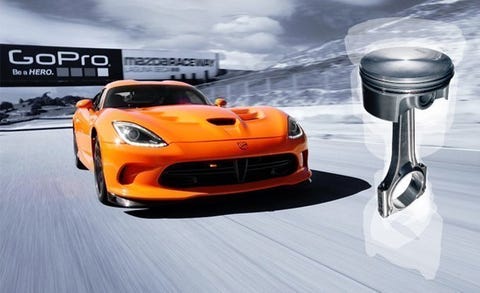
Applications: Dodge Viper (shown)
Engine Type: pushrod V-10
Displacement: 512 cu in, 8382 cc
Specific Output: 76.4 hp/l
Max engine speed: 6400 rpm
Bore: 4.06 in
Weight: 2.8 lb
Ford EcoBoost 3.5L
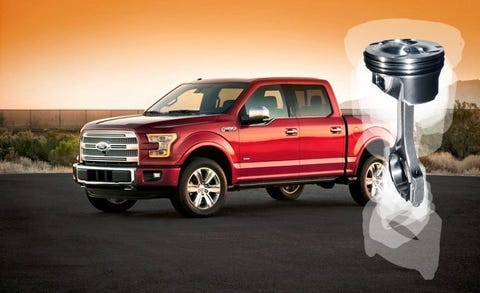
Applications: Ford Expedition, Explorer Sport, F-150 (shown), Taurus SHO, Transit; Lincoln MKS, MKT, Navigator
Engine Type: twin-turbocharged DOHC V-6
Displacement: 213 cu in, 3496 cc
Specific Output: up to 105.8 hp/l
Max engine speed: 6500 rpm
Bore: 3.64 in
Weight: 2.6 lb
Toyota 2AR-FE
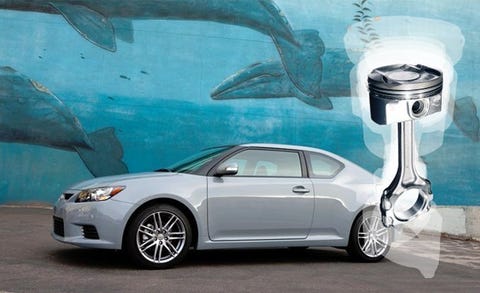
Applications: Scion tC (shown); Toyota Camry, RAV4
Engine Type: DOHC inline-four
Displacement: 152 cu in, 2494 cc
Specific Output: up to 72.2 hp/l
Max engine speed: 6500 rpm
Bore: 3.54 in
Weight: 2.5 lb
Stihl MS441 Chain Saw
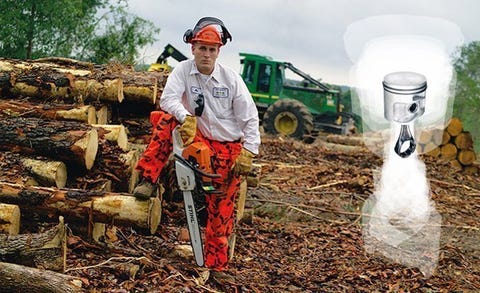
Applications: MS441 C-M Magnum chain saw (shown), MS441 C-MQ Magnum chain saw
Engine Type: two-stroke single-cylinder
Displacement: 4 cu in, 71 cc
Specific Output: 79.7 hp/l
Max engine speed: 13,500 rpm
Bore: 1.97 in
Weight: 0.4 lb
Chrysler Hellcat 6.2L
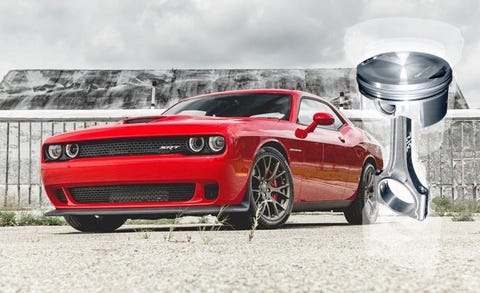
Applications: Dodge Challenger SRT Hellcat
Engine Type: supercharged pushrod V-8
Displacement: 376 cu in, 6166 cc
Specific Output: 114.7 hp/l
Max engine speed: 6200 rpm
Bore: 4.09 in
Weight: 3.0 lb
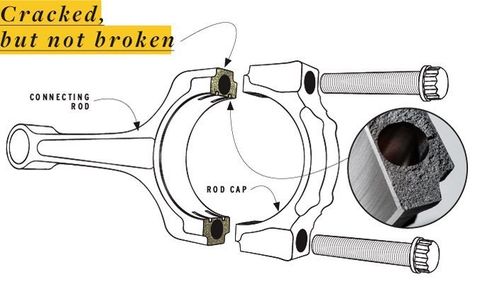
As the workload for pistons increases, so do the demands on connecting rods. Higher combustion pressures translate to greater stresses on the sticks linking the pistons to the crank. Mit der seltenen Ausnahme von exotischen Titanstücken werden Pleuelstangen in der Regel entweder aus pulverisiertem Stahl hergestellt, der in einer Form gepresst und erhitzt wird, oder für Hochleistungsanwendungen aus Stahl geschmiedet. Der größte technologische Wandel besteht in geknackten Big-End-Kappen sowohl für Pulvermetall- als auch für geschmiedete Pleuelstangen. Früher wurden die Stange und die Kurbelzapfenkappe als separate Teile hergestellt. Stangen mit gebrochenen Kappen kommen als ein einziges, kastenförmiges Teil aus der Form. Das Kurbelzapfenende wird geätzt und dann mit einer Presse in zwei Teile geteilt. Die sich daraus ergebende unregelmäßige Oberfläche verbessert die Ausrichtung, sorgt für eine sicherere Verbindung zwischen Kappe und Stange und ermöglicht eine schlankere, leichtere Pleuel-Baugruppe.
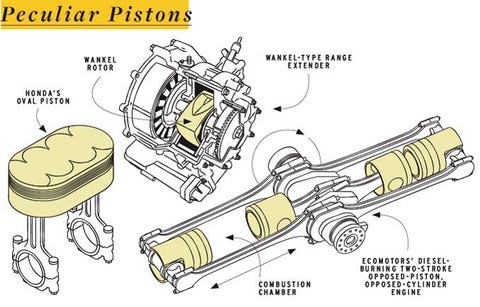
Nichtmetallische Kolben: Keramik und Verbundwerkstoffe locken mit geringerer Wärmeausdehnung, geringerem Gewicht und höherer Festigkeit und Steifigkeit im Vergleich zu Aluminium. In den 1980er Jahren nutzte Mercedes-Benz einen Zuschuss der deutschen Regierung, um einen 190E-Motor mit Kolben aus Kohlefaserverbundwerkstoffen zu entwickeln, der 15.000 Meilen lang ohne Probleme lief. Die Technologie ist zwar solide, aber die Herstellung war der begrenzende Faktor. Eine NASA-Studie aus dem Jahr 1990 ergab, dass die Bearbeitung eines einzelnen Kolbens aus einem Kohlenstoff-Kohlenstoff-Block 2.000 Dollar kostete. Die Alternative war ein zeitaufwändiges Handauflegeverfahren.
Wankel-Rotoren: Okay, okay, wir wissen, dass es sich nicht um einen Hubkolben handelt, aber der gusseiserne dreieckige Rotor ist das Analogon des Wankelmotors, weil er die Verbrennungsenergie in Drehmoment umwandelt. Da kein neuer Mazda RX in Sicht ist, scheint unsere einzige Hoffnung auf eine Wiederbelebung des Wankelmotors Audi zu sein, der uns in seinem Plug-in-Hybrid-Konzept für den Audi A1 e-tron von 2010 einen Wankelmotor als Range Extender präsentiert hat.
Ovalkolben: In einer Zeit, in der Zweitakt-Motorradmotoren die Norm waren, brachte Honda 1979 einen Viertaktmotor zum World Motorcycle Grand Prix. Er gilt als einer der seltsamsten Motoren der Geschichte. Hondas NR500 GP-Motorrad wurde von einem V-4-Motor mit einem Bögenwinkel von 100 Grad, ovalen Zylindern mit jeweils acht Ventilen und zwei Pleuelstangen pro Kolben angetrieben. Die Abdichtung der ovalen Kolben erwies sich als schwierig (Soichiro Hondas ursprüngliches Geschäft war die Lieferung von Kolbenringen an Toyota), aber das war mit die geringste Sorge des Teams. Die Motorräder schieden regelmäßig bei Welt-GP-Rennen aus und schafften es gelegentlich nicht, sich zu qualifizieren. Innerhalb von drei Jahren kehrte Honda zu einem traditionellen Zweitakt-Rennmotor zurück.
Opposed-Piston-Motoren: Der dieselbetriebene Zweitakt-Oppositionskolbenmotor (OPOC) von EcoMotors verspricht eine Effizienzsteigerung von bis zu 15 Prozent gegenüber einem herkömmlichen Selbstzündungsmotor. Durch die Platzierung der Verbrennungskammer zwischen zwei Kolben hat das Unternehmen die Zylinderköpfe und den Ventiltrieb eliminiert, die Quellen erheblicher Wärmeverluste und Reibung sind. Ein OPOC-Motor mit weniger Teilen sollte auch billiger und leichter sein, wenn er nicht zusammen mit dem fantastischen Fischvergaser im Regal landet.