Basiskennis
Wat is spuitgieten en hoe heeft het zich ontwikkeld sinds de 19e eeuw? Dit en vele andere basisprincipes zoals het gebruik van verschillende processen en materialen worden uitgelegd in het volgende artikel.
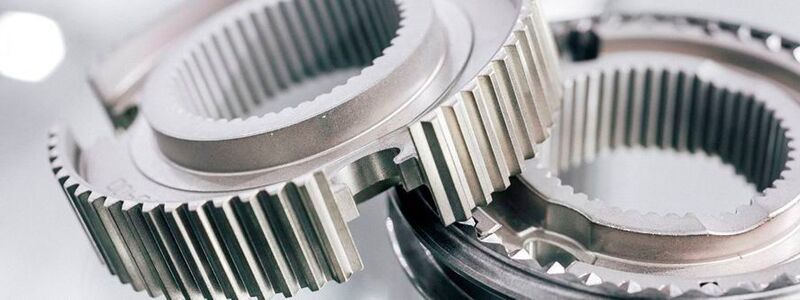
Gietwerk is een van de meest economische en snelste vormingsprocessen. De voordelen van dit productieproces zijn dat met slechts één matrijs relatief snel honderdduizenden gietstukken kunnen worden geproduceerd. Alle geproduceerde onderdelen hebben een uniforme kwaliteit en brengen relatief lage eenheidskosten met zich mee. Maar hoe ziet het fabricageproces er precies uit? Welke materialen kunnen worden gebruikt en op welke gebieden worden de gietstukken gebruikt?
Definitie van “Die Casting”
Gietwerk is een geautomatiseerd gietproces waarbij de vloeibare smelt onder hoge druk (150 tot 1200 bar) en met een hoge vulsnelheid (tot 540 km/u) in een matrijs wordt geperst. Gewoonlijk worden legeringen met een laag smeltpunt gebruikt. Dit gietprocédé is bijzonder geschikt voor serie- en massaproductie van onderdelen omdat, in tegenstelling tot bijvoorbeeld zandgieten, permanente metalen mallen worden gebruikt die na het gieten niet hoeven te worden vernietigd. Het is mogelijk om grote en complexe onderdelen met geringe wanddiktes te produceren.
#expert
:quality(80)/images.vogel.de/vogelonline/bdb/1420000/1420060/original.jpg)
Mallen
De spuitgietmatrijzen, gemaakt van hoogwaardige, hittebestendige staalsoorten, bestaan uit twee helften die een holte vormen waarin de vloeibare smelt tijdens het gietproces wordt geperst. De helften bevinden zich op een vaste en een beweegbare machineplaat. Tijdens het gietproces wordt een hoge druk uitgeoefend op de matrijshelften; daarom is de matrijs voorzien van sluitingen. Bovendien worden bepaalde delen van de matrijs gekoeld en/of verwarmd, zodat het gietstuk naar wens stolt. De productie van de matrijzen is zeer duur en tijdrovend, maar met één enkele matrijs kunnen enkele tienduizenden tot meer dan een miljoen gietstukken worden vervaardigd. Een ander voordeel van de herbruikbare gietvormen is dat de smelt snel afkoelt.
Functionaliteit en procedures
Bij het spuitgieten zijn er twee verschillende manieren om onderdelen te vervaardigen: het spuitgieten met een warme kamer en het spuitgieten met een koude kamer. Bij beide fabricageprocessen wordt de gietvorm vóór het gietproces bespoten met een lossingsmiddel om ervoor te zorgen dat het daarna gegoten onderdeel gemakkelijk uit de gietvorm kan worden verwijderd. De smelt wordt echter niet rechtstreeks in de vormholte gegoten, maar wordt eerst in de gietkamer van de spuitgietmachine gevuld. Van daaruit wordt de legering door een zuiger (de zogenaamde gietset) via een of meer kanalen in de matrijs geperst. Het verschil tussen de twee processen ligt in de structuur van de gietkamer, zoals hieronder beschreven.
Hotkamergietmethode
Een karakteristiek kenmerk van hotkamergietmachines is dat de gietkamer voortdurend in contact staat met de vloeibare legering. De smelt gaat door een klep in de gietkamer, waar het met hoge snelheid in de gesloten gietvorm wordt geperst door de zuiger. Dit proces wordt gebruikt voor legeringen met een laag smeltpunt, zoals zink, lood of tin.
Koudkamergietmethode
Koudkamergietmachines zijn zo ontworpen dat de gietset zich buiten de smelt bevindt. Om een component te produceren, wordt de legering in de gietkamer gevuld en door kanalen in de matrijzen gietvorm geperst. Dit proces is geschikt voor materialen met een hoger smeltpunt. Hiertoe behoren bijvoorbeeld aluminium en koper.
Nadat de legering in beide processen in de matrijs is geperst, stolt het onderdeel onder de sterke druk, waarna de grendels van de matrijs kunnen worden geopend. Het onderdeel met poort wordt door automatisch bediende uitwerppennen uit de matrijs verwijderd en kan zo nodig verder worden bewerkt. Het gietproces kan eenvoudigweg in de volgende stappen worden onderverdeeld en vindt in de praktijk plaats in honderdsten van een seconde – of zelfs slechts duizendsten van een seconde:
- Snel vullen van de gietvorm met de legering
- Harden van het onderdeel onder hoge druk
- Openen van de gietvorm en verwijderen van het onderdeel
:quality(80)/images.vogel.de/vogelonline/bdb/1506300/1506374/original.jpg)
Koudkamergieten is het populairste proces voor de massaproductie van lichtmetaalgietwerk. Lees nu over de belangrijkste factoren voor het realiseren van een kostenbesparend lichtgewicht ontwerpconcept.
Materialen1
Bij het spuitgieten worden non-ferrometalen gebruikt om onderdelen te vervaardigen, en de keuze van de legering voor een bepaalde toepassing is afhankelijk van budget, gewicht en materiaaleigenschappen.
Aluminium is een van de belangrijkste materialen met een aandeel van meer dan 80 %, gevolgd door zink en magnesium. However, copper, lead and tin can also be used. The alloys have different properties. For example, aluminum (600°C) and magnesium (520°C) have a high melting point, zinc (380°C) and lead (320°C) a low melting point.
Die casting alloys offer many advantages:
- High corrosion resistance
- High strength and hardness
- High thermal conductivity
- High electrical conductivity
- Very good EMI/ RFI isolation
- Good processing properties
:quality(80)/images.vogel.de/vogelonline/bdb/1317600/1317687/original.jpg)
Low-Pressure vs. High-Pressure Die Casting
Various processes are used in foundry practice. Castings can also be produced without high pressure. In the sand casting process, for example, the alloy is poured into a mold made of sand, which must be destroyed in order to reveal the manufactured component (lost foam). Bij verlorenwasgieten, dat wordt gebruikt om zeer kleine gegoten onderdelen te vervaardigen, worden de mallen en modellen (meestal van was of plastic) na het gietproces eveneens vernietigd. Een ander voorbeeld is het zwaartekracht-gietproces, waarbij een permanente metalen mal wordt gebruikt, maar geen hoge druk wordt uitgeoefend om de smelt in de mal te persen. In plaats daarvan wordt het gietstuk vervaardigd of wordt de mal gevuld door de zwaartekracht.
Er zijn ook verschillen in het spuitgietproces. Zo zijn er processen die ofwel hoge ofwel lage druk gebruiken om de onderdelen te produceren. Terwijl het hogedrukgieten goed is voor ongeveer 50% van de productie van het gieten van lichte metalen, vertegenwoordigt het lagedrukgieten slechts iets minder dan 20% van de totale productie.2
Het lagedrukgieten maakt hoofdzakelijk gebruik van legeringen met een laag smeltpunt. Er kunnen onderdelen van 2 tot 150 kg worden gegoten. De voordelen zijn dat zeer hoge sterktes en complexe geometrieën kunnen worden bereikt en dat het materiaalgebruik en de maatnauwkeurigheid kunnen worden verbeterd. Het procédé is minder geschikt voor zeer dunwandige onderdelen, aangezien slechts een minimale wanddikte van 3 mm kan worden verkregen. Ook moet worden vermeld dat de gietcycli bij lagedrukgieten langzamer zijn dan bij hogedrukgieten.
Bij hogedrukgieten wordt de smelt onder hoge druk en met hoge snelheid in de gietvorm geperst, waardoor de gietcyclus wordt versneld. Bovendien kunnen dunnere gietstukken (minimale wanddikte van 1 mm) met gladdere oppervlakken worden vervaardigd. Het nadeel van dit fabricageproces is echter dat hoge bedrijfs- en investeringskosten ontstaan, de sterktewaarden lager zijn en het gietgewicht beperkt is omdat het afhankelijk is van de sluitkracht van de machine.
:quality(80)/images.vogel.de/vogelonline/bdb/1508700/1508781/original.jpg)
Toepassingsgebieden
Gietwerk wordt voornamelijk gebruikt voor grote serieproductie, d.w.z. voor het gieten van vele onderdelen van hetzelfde type. Despite the high pressure used during the manufacturing process, a high casting quality is achieved. The die casting process is particularly suitable for the production of very thin (up to 1 mm) (lightweight) components.
Most commonly, die cast components are manufactured for the automotive industry, such as wheels, blocks, cylinder heads, valve blocks and manifolds. This sector accounts for around 84 % of the castings produced by German foundries. 3 The use of aluminum parts leads to a reduction in the weight of the vehicles and thus to a reduction in fuel consumption. In addition, there are other industries in which die cast parts are used:
- Aerospace
- Domestic Appliances
- Furniture
- Power Tools
- Electronics
- Machinery
- Lighting Technology
In the future, other industries such as electromobility will be of interest to foundries. Dit biedt enorme mogelijkheden voor het gieten van lichte metalen.4
Geschiedenis van het spuitgieten 5
Het spuitgieten is ontstaan in het midden van de 19e eeuw, toen de uitgeverij tot bloei kwam. Het doel was om kranten en boeken snel, flexibel en kosteneffectief te kunnen drukken. Zo kwam er een met de hand bediend apparaat waarmee een legering van tin en lood in letters kon worden gegoten (1838), de rotatiedrukpers (1846) en tenslotte de zetmachine Linotype (1886). Een van de belangrijkste elementen van deze machine was een geïntegreerde spuitgietmachine die vloeibaar lood in de lijnmallen van messing lettermatrijzen goot. Na het gieten werden de matrijzen teruggebracht naar het matrijzenmagazijn en werden de gegoten loden lijnen uitgeworpen. De loden lijnen werden vervolgens samengevoegd tot pagina’s die dienden als drukplaten voor vellendruk of als sjablonen voor de ronde drukplaten die nodig waren voor het rotatiedrukproces.
:quality(80)/images.vogel.de/vogelonline/bdb/1475800/1475868/original.jpg)
Tijdens de eerste 30 jaar werd het spuitgieten vrijwel uitsluitend gebruikt in de drukindustrie. Het keerpunt kwam toen Herman H. Doehler in 1908 de Doehler Die Casting Company oprichtte, die in het begin van de jaren 1940 als ’s werelds grootste fabrikant van spuitgietonderdelen werd beschouwd en tot 1998 heeft bestaan. De eerste spuitgietmachine op de markt, die alle essentiële onderdelen van een moderne spuitgietmachine bevatte, werd in 1925 ontwikkeld door Joseph Soss en Louis H. Morin in de VS.
Tijdens het eind van de 19e eeuw en de eerste decennia van de 20e eeuw kwamen er nieuwe producten op de markt en groeide de industriële productie snel. Fabrikanten erkenden de voordelen van spuitgieten, dat kon worden gebruikt om op economische wijze onderdelen te produceren voor schrijfmachines, kassa’s, horloges en elektrische apparaten. Speelgoedfabrikanten gebruikten ook spuitgieten om speelgoed- en modelauto’s te produceren die zo getrouw mogelijk waren aan het origineel. Last but not least werden de opkomende automobielindustrie en haar toeleveranciers belangrijke afnemers van spuitgietproducten.
Sinds het begin van de 20e eeuw is de spuitgiettechnologie steeds sneller vooruitgegaan. Aanvankelijk werden vooral lood en tin, twee metalen met een relatief lage smelttemperatuur en een goede vervormbaarheid, gebruikt bij het spuitgieten. Rond 1914 begon men te werken aan zink- en aluminiumlegeringen, die hogere sterktes boden. Koper- en magnesiumlegeringen werden in de jaren 1930 toegevoegd. Magnesium, dat met een soortelijk gewicht van 1,74 g/cm3 een derde minder weegt dan het lichte metaal aluminium (2,75 g/cm3) en tegenwoordig vooral in de automobielindustrie wordt gebruikt, beleefde zijn eerste opgang als spuitgietmateriaal tussen 1946 en 1978: Motor en versnellingsbak van de VW Kever werden van dit materiaal gemaakt. De spuitgiettechnologie bleef echter niet op dit ontwikkelingsniveau hangen. De machines werden uitgerust met een verfijnde besturingstechniek en werden steeds krachtiger. Gereedschapsstaal met verbeterde eigenschappen kwam op de markt voor het maken van matrijzen, en de fysische eigenschappen van spuitgietlegeringen werden geoptimaliseerd, zodat vandaag gietstukken met zowel zeer dunne wanddikten als hoge mechanische eigenschappen kunnen worden geproduceerd. Actuele onderwerpen zijn automatisering, energie- en grondstofefficiëntie, complexe vormen, hybride onderdelen, procesautomatisering en digitalisering (Industrie 4.0).
:quality(80)/images.vogel.de/vogelonline/bdb/1518000/1518051/original.jpg)
1) Dynacast, gegoten metalen, verkrijgbaar op https://www.dynacast.de/druckgussmetalle-al-mg-zn
2) The Metal Casting, beschikbaar op http://www.themetalcasting.com/pressure-die-casting.html
3) BD Guss, 2016
4) NürnbergMesse, 2018, beschikbaar op https://www.euroguss.de/de/news/presseinformationen/zukunft-von-druckguss-7sxvrxjjb7_pireport
5) NürnbergMesse, 2018, available on https://www.euroguss.de/de/news/fachartikel/fachartikel-druckgiessen-nl2jm1fcex_pireport
Further References
KUG BD Guss, 2009, Die Casting – Series production for highly complex thin-walled light metal castings, available on https://www.kug.bdguss.de/giessverfahren-inhalte/druckguss/
Powerguss – Haus der Gießerei-Industrie, Die casting – how does it work?, available on https://www.powerguss.de/was-ist-giessen/druckguss/
Lechuga, G., 2016, Die Casting Facts Infographic, available on https://www.slideshare.net/GermnLechuga/die-casting-facts-infographic
Dynacast, die casting, available on https://www.dynacast.de/druckguss