Cunoștințe de bază
Ce este turnarea sub presiune și cum a progresat din secolul al XIX-lea? Acest lucru și multe alte noțiuni de bază, cum ar fi utilizarea diferitelor procese și materiale, sunt explicate în următorul articol.
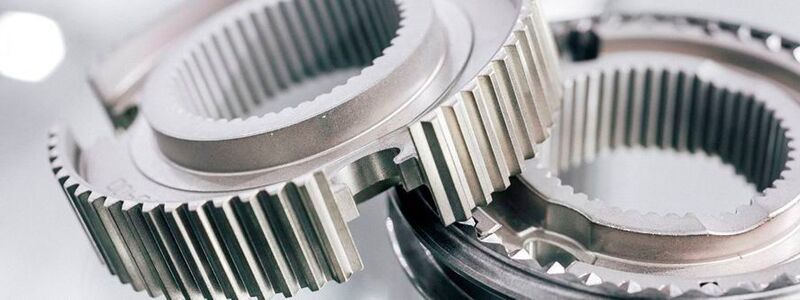
Colația în matriță este unul dintre cele mai economice și mai rapide procese de formare. Avantajele acestui proces de producție constau în faptul că sute de mii de piese turnate pot fi produse relativ rapid prin utilizarea unei singure matrițe. Toate componentele produse au o calitate uniformă și implică costuri unitare relativ scăzute. Dar cum arată mai exact procesul de fabricație? Ce materiale pot fi folosite și în ce domenii se folosesc piesele turnate?
Definiția „turnării sub presiune”
Turnarea sub presiune este un proces automatizat de turnare în care lichidul topit este presat într-o matriță sub presiune ridicată (150 până la 1200 bar) și la o viteză mare de umplere (până la 540 km/h). De obicei, se utilizează aliaje cu un punct de topire scăzut. Acest proces de turnare este deosebit de potrivit pentru producția în serie și în masă a componentelor, deoarece, spre deosebire de turnarea în nisip, de exemplu, se folosesc matrițe metalice permanente care nu trebuie distruse după turnare. Este posibil să se producă componente mari și complexe cu grosimi reduse ale pereților.
#expert
:quality(80)/images.vogel.de/vogelonline/bdb/1420000/1420060/original.jpg)
Modelurile
Modelurile de turnare sub presiune, realizate din oțeluri de înaltă calitate, rezistente la căldură, sunt compuse din două jumătăți care formează o cavitate în care lichidul topit este presat în timpul procesului de turnare. Jumătățile sunt amplasate pe o placă de mașină fixă și una mobilă. În timpul procesului de turnare se aplică o presiune ridicată asupra jumătăților matriței, motiv pentru care matrița este echipată cu zăbrele. În plus, anumite părți ale matriței sunt răcite și/sau încălzite pentru ca turnarea să se solidifice așa cum se dorește. Producția matrițelor este foarte costisitoare și consumatoare de timp, dar cu una singură se pot produce de la câteva zeci de mii până la peste un milion de piese turnate. Un alt avantaj al matrițelor de turnare reutilizabile este că topitura se răcește rapid.
Funcționalitate și proceduri
În turnarea sub presiune, există două moduri diferite de a fabrica componente: turnarea sub presiune cu cameră caldă și turnarea sub presiune cu cameră rece. În ambele procese de fabricație, matrița este pulverizată cu un agent de degajare înainte de procesul de turnare pentru a se asigura că piesa turnată ulterior poate fi îndepărtată cu ușurință din matriță. Cu toate acestea, masa topită nu este turnată direct în cavitatea matriței, ci este mai întâi umplută în camera de turnare a mașinii de turnare sub presiune. De acolo, aliajul este presat în matriță de un piston (așa-numitul set de turnare) prin unul sau mai multe canale. Diferența dintre cele două procese constă în structura camerei de turnare, așa cum este descrisă mai jos.
Metoda de turnare sub presiune cu cameră caldă
O trăsătură caracteristică a mașinilor de turnare sub presiune cu cameră caldă este faptul că camera de turnare este în permanență în contact cu aliajul lichid. Topitura trece printr-o supapă în camera de turnare, unde este presată la viteză mare în matrița închisă de turnare sub presiune de către piston. Acest proces este utilizat pentru aliajele cu un punct de topire scăzut, cum ar fi zincul, plumbul sau staniul.
Metoda de turnare sub presiune cu cameră rece
Mașinile de turnare sub presiune cu cameră rece sunt proiectate în așa fel încât setul de turnare să fie situat în afara topiturii. Pentru a produce o componentă, aliajul este umplut în camera de turnare și presat în matrița de turnare sub presiune prin canale. Acest procedeu este potrivit pentru materialele cu un punct de topire mai ridicat. Printre acestea se numără, de exemplu, aluminiul și cuprul.
După ce aliajul a fost presat în matriță în ambele procese, componenta se solidifică sub presiunea puternică, după care zăvoarele matriței pot fi deschise. Piesa cu poartă este scoasă din matriță cu ajutorul unor pini de ejecție acționați automat și poate fi prelucrată în continuare, dacă este necesar. Cu cuvinte simple, procesul de turnare poate fi împărțit în următoarele etape și, în practică, se desfășoară în sutimi de secundă – sau chiar numai miimi de secundă:
- Umplerea rapidă a formei de turnare cu aliajul
- Curățarea componentei sub presiune înaltă
- Deschiderea formei și îndepărtarea componentei
:quality(80)/images.vogel.de/vogelonline/bdb/1506300/1506374/original.jpg)
Cojirea sub presiune în cameră rece este cel mai popular proces în producția de masă a pieselor turnate din metale ușoare. Citiți acum despre factorii cheie pentru realizarea unui concept de design ușor cu costuri reduse.
Materiale1
În turnarea sub presiune, pentru fabricarea componentelor se folosesc metale neferoase, iar alegerea aliajului pentru o anumită aplicație depinde de buget, greutate și proprietăți ale materialului.
Aluminiul este unul dintre cele mai importante materiale, cu o pondere de peste 80 %, urmat de zinc și magneziu. However, copper, lead and tin can also be used. The alloys have different properties. For example, aluminum (600°C) and magnesium (520°C) have a high melting point, zinc (380°C) and lead (320°C) a low melting point.
Die casting alloys offer many advantages:
- High corrosion resistance
- High strength and hardness
- High thermal conductivity
- High electrical conductivity
- Very good EMI/ RFI isolation
- Good processing properties
:quality(80)/images.vogel.de/vogelonline/bdb/1317600/1317687/original.jpg)
Low-Pressure vs. High-Pressure Die Casting
Various processes are used in foundry practice. Castings can also be produced without high pressure. In the sand casting process, for example, the alloy is poured into a mold made of sand, which must be destroyed in order to reveal the manufactured component (lost foam). În turnarea cu investiții, care este utilizată pentru fabricarea pieselor turnate foarte mici, matrițele și modelele (de obicei din ceară sau plastic) sunt, de asemenea, distruse după procesul de turnare. Un alt exemplu este turnarea prin gravitație, care utilizează o matriță metalică permanentă, dar nu folosește o presiune ridicată pentru a presa topitura în matriță. Mai degrabă, turnarea este fabricată sau matrița este umplută prin gravitație.
Există, de asemenea, diferențe în procesul de turnare sub presiune. De exemplu, există procese care folosesc fie presiune ridicată, fie presiune scăzută pentru a produce componentele. În timp ce turnarea sub presiune înaltă reprezintă aproximativ 50 % din producția de turnare a metalelor ușoare, turnarea sub presiune joasă reprezintă doar puțin sub 20 % din producția totală.2
Pentru turnarea sub presiune joasă se folosesc în principal aliaje cu puncte de topire scăzute. Este posibil să se toarne componente de la 2 la 150 kg. Avantajele constau în faptul că se pot obține valori foarte ridicate ale rezistenței și geometrii complexe, precum și o mai bună utilizare a materialului și precizie dimensională. Procesul este mai puțin potrivit pentru piesele cu pereți foarte subțiri, deoarece se poate obține doar o grosime minimă a peretelui de 3 mm. De asemenea, trebuie menționat că ciclurile de turnare care utilizează turnarea sub presiune joasă sunt mai lente decât cele sub presiune înaltă.
În turnarea sub presiune înaltă, topitura este presată în matriță sub presiune înaltă și la viteză mare, accelerând astfel ciclul de turnare. În plus, se pot produce piese turnate cu pereți mai subțiri (grosimea minimă a peretelui de 1 mm) cu suprafețe mai netede. Dezavantajul acestui procedeu de fabricație este însă că se înregistrează costuri ridicate de exploatare și de investiție, valorile de rezistență sunt mai mici, iar greutatea piesei turnate este limitată, deoarece depinde de forța de închidere a mașinii.
:quality(80)/images.vogel.de/vogelonline/bdb/1508700/1508781/original.jpg)
Domenii de aplicare
Turnarea în matriță este folosită în principal pentru producția de serie mare, adică pentru turnarea mai multor componente de același tip. Despite the high pressure used during the manufacturing process, a high casting quality is achieved. The die casting process is particularly suitable for the production of very thin (up to 1 mm) (lightweight) components.
Most commonly, die cast components are manufactured for the automotive industry, such as wheels, blocks, cylinder heads, valve blocks and manifolds. This sector accounts for around 84 % of the castings produced by German foundries. 3 The use of aluminum parts leads to a reduction in the weight of the vehicles and thus to a reduction in fuel consumption. In addition, there are other industries in which die cast parts are used:
- Aerospace
- Domestic Appliances
- Furniture
- Power Tools
- Electronics
- Machinery
- Lighting Technology
In the future, other industries such as electromobility will be of interest to foundries. Acest lucru oferă un potențial enorm pentru piesele turnate din metale ușoare.4
Istoria turnării sub presiune 5
Turnarea sub presiune a luat naștere la mijlocul secolului al XIX-lea, când a înflorit industria editorială. Scopul era de a putea tipări ziare și cărți în mod rapid, flexibil și eficient din punct de vedere al costurilor. Printre acestea se numără un dispozitiv acționat manual în care un aliaj de staniu și plumb putea fi turnat în litere (1838), presa tipografică rotativă (1846) și, în cele din urmă, mașina de tipărire Linotype (1886). Unul dintre elementele principale ale acestei mașini a fost o mașină de turnare integrată care turna plumb lichid în matrițele de linie realizate din matrițe de litere din alamă. După turnare, matrițele erau returnate în magazia de matrițe, iar liniile de plumb turnate erau ejectate. Liniile de plumb erau apoi asamblate în pagini care serveau ca plăci de tipar pentru tipărirea pe foi sau ca șabloane pentru plăcile rotunde necesare pentru procesul de tipărire rotativă.
:quality(80)/images.vogel.de/vogelonline/bdb/1475800/1475868/original.jpg)
În primii 30 de ani, turnarea sub presiune a fost utilizată practic exclusiv în industria tipografică. Momentul de cotitură a avut loc atunci când Herman H. Doehler a fondat în 1908 compania Doehler die casting Company, care la începutul anilor 1940 era considerată cel mai mare producător de piese turnate sub presiune din lume și a existat până în 1998. Prima mașină de turnare sub presiune disponibilă pe piață, care conținea toate componentele esențiale ale unei mașini moderne de turnare sub presiune, a fost dezvoltată în 1925 de Joseph Soss și Louis H. Morin în SUA.
În timpul sfârșitului secolului al XIX-lea și al primelor decenii ale secolului al XX-lea, noi produse au apărut pe piață, iar producția industrială a crescut rapid. Producătorii au recunoscut avantajele turnării sub presiune, care putea fi folosită pentru a produce în mod economic piese pentru mașini de scris, case de marcat, ceasuri și aparate electrice. Producătorii de jucării au folosit, de asemenea, turnarea sub presiune pentru a produce mașini de jucărie și machete care erau cât se poate de fidele la original. Nu în ultimul rând, industria auto emergentă și furnizorii acesteia au devenit cumpărători importanți de produse turnate sub presiune.
De la începutul secolului XX, tehnologia de turnare sub presiune a progresat cu o viteză din ce în ce mai mare. Inițial, la turnarea sub presiune se foloseau în principal plumbul și staniul, două metale cu o temperatură de topire relativ scăzută și o ductilitate bună. În jurul anului 1914, au început lucrările la aliajele de zinc și aluminiu, care ofereau o rezistență mai mare. Aliajele de cupru și magneziu au fost adăugate în anii 1930. Magneziul, care, cu o densitate specifică de 1,74 g/cm3, cântărește cu o treime mai puțin decât metalul ușor aluminiu (2,75 g/cm3) și este utilizat astăzi în principal în industria automobilelor, a cunoscut primul său boom ca material de turnare sub presiune între 1946 și 1978: Motorul și cutia de viteze a modelului VW Beetle au fost realizate din acest material. Cu toate acestea, tehnologia de turnare sub presiune nu a zăbovit la acest nivel de dezvoltare. Mașinile au fost dotate cu o tehnologie de control rafinată și au devenit din ce în ce mai puternice. Au apărut pe piață oțeluri pentru scule cu proprietăți îmbunătățite pentru fabricarea matrițelor, iar proprietățile fizice ale aliajelor de turnare sub presiune au fost optimizate, astfel încât astăzi pot fi produse piese turnate atât cu grosimi de perete foarte subțiri, cât și cu proprietăți mecanice ridicate. Printre subiectele actuale se numără automatizarea, eficiența energetică și a materiilor prime, formele complexe, piesele hibride, automatizarea proceselor și digitalizarea (Industria 4.0).
:quality(80)/images.vogel.de/vogelonline/bdb/1518000/1518051/original.jpg)
1) Dynacast, metale turnate sub presiune, disponibile pe https://www.dynacast.de/druckgussmetalle-al-mg-zn
2) The Metal Casting, disponibil pe http://www.themetalcasting.com/pressure-die-casting.html
3) BD Guss, 2016
4) NürnbergMesse, 2018, disponibil pe https://www.euroguss.de/de/news/presseinformationen/zukunft-von-druckguss-7sxvrxjjb7_pireport
5) NürnbergMesse, 2018, available on https://www.euroguss.de/de/news/fachartikel/fachartikel-druckgiessen-nl2jm1fcex_pireport
Further References
KUG BD Guss, 2009, Die Casting – Series production for highly complex thin-walled light metal castings, available on https://www.kug.bdguss.de/giessverfahren-inhalte/druckguss/
Powerguss – Haus der Gießerei-Industrie, Die casting – how does it work?, available on https://www.powerguss.de/was-ist-giessen/druckguss/
Lechuga, G., 2016, Die Casting Facts Infographic, available on https://www.slideshare.net/GermnLechuga/die-casting-facts-infographic
Dynacast, die casting, available on https://www.dynacast.de/druckguss