Conocimientos básicos
¿Qué es la fundición a presión y cómo ha ido progresando desde el siglo XIX? Esto y muchos otros aspectos básicos, como el uso de diferentes procesos y materiales, se explican en el siguiente artículo.
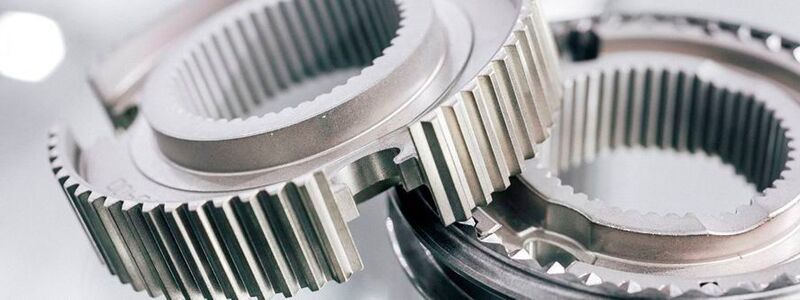
La fundición en molde es uno de los procesos de conformación más económicos y rápidos. Las ventajas de este proceso de producción son que se pueden producir cientos de miles de piezas fundidas con relativa rapidez utilizando un solo molde. Todos los componentes producidos tienen una calidad uniforme y suponen unos costes unitarios relativamente bajos. Pero, ¿cómo es exactamente el proceso de fabricación? ¿Qué materiales se pueden utilizar y en qué áreas se utilizan las piezas fundidas?
Definición de «Die Casting»
El «Die Casting» es un proceso de fundición automatizado en el que la masa fundida líquida se presiona en un molde a alta presión (de 150 a 1200 bar) y a una alta velocidad de llenado (hasta 540 km/h). Normalmente se utilizan aleaciones con un punto de fusión bajo. Este proceso de fundición es especialmente adecuado para la producción en serie y en masa de componentes porque, a diferencia de la fundición en arena, por ejemplo, se utilizan moldes metálicos permanentes que no tienen que destruirse después de la fundición. Es posible producir componentes grandes y complejos con espesores de pared bajos.
#expert
:quality(80)/images.vogel.de/vogelonline/bdb/1420000/1420060/original.jpg)
Moldes
Los moldes de fundición a presión, fabricados con aceros de alta calidad y resistentes al calor, constan de dos mitades que forman una cavidad en la que se presiona el líquido fundido durante el proceso de fundición. Las mitades están situadas en una placa de máquina fija y otra móvil. Durante el proceso de fundición se aplica una alta presión a las mitades del molde, por lo que éste está equipado con pestillos. Además, algunas partes del molde se enfrían y/o se calientan para que la colada se solidifique como se desea. La producción de los moldes es muy costosa y requiere mucho tiempo, pero con uno solo de ellos se pueden producir desde varias decenas de miles hasta más de un millón de piezas de fundición. Otra ventaja de los moldes de fundición reutilizables es que la masa fundida se enfría rápidamente.
Funcionalidad y procedimientos
En la fundición a presión, hay dos formas diferentes de fabricar componentes: la fundición a presión en cámara caliente y en cámara fría. En ambos procesos de fabricación, el molde se rocía con un agente desmoldante antes del proceso de fundición para asegurar que la pieza posteriormente fundida pueda ser fácilmente extraída del molde. Sin embargo, la masa fundida no se vierte directamente en la cavidad del molde, sino que primero se llena la cámara de fundición de la máquina de fundición a presión. A partir de ahí, la aleación se introduce a presión en el molde mediante un pistón (el llamado conjunto de fundición) a través de uno o varios canales. La diferencia entre ambos procesos radica en la estructura de la cámara de fundición, como se describe a continuación.
Método de fundición a presión con cámara caliente
Un rasgo característico de las máquinas de fundición a presión con cámara caliente es que la cámara de fundición está constantemente en contacto con la aleación líquida. La masa fundida pasa a través de una válvula a la cámara de fundición, donde es presionada a alta velocidad en el molde de fundición a presión cerrado por el pistón. Este proceso se utiliza para aleaciones con un punto de fusión bajo, como el zinc, el plomo o el estaño.
Método de fundición a presión en cámara fría
Las máquinas de fundición a presión en cámara fría están diseñadas de tal manera que el conjunto de fundición se encuentra fuera de la masa fundida. Para producir un componente, la aleación se llena en la cámara de fundición y se presiona en el molde de fundición a presión a través de canales. Este proceso es adecuado para materiales con un punto de fusión más alto. Entre ellos se encuentran, por ejemplo, el aluminio y el cobre.
Después de que la aleación haya sido prensada en el molde en ambos procesos, el componente se solidifica bajo la fuerte presión, con lo que se pueden abrir los cierres del molde. La pieza con la compuerta se extrae del molde mediante pasadores de expulsión de accionamiento automático y puede seguir procesándose si es necesario. En palabras sencillas, el proceso de fundición puede dividirse en los siguientes pasos y, en la práctica, tiene lugar en centésimas de segundo, o incluso en milésimas de segundo:
- Relleno rápido del molde de fundición con la aleación
- Curación del componente bajo alta presión
- Apertura del molde y retirada del componente
- High corrosion resistance
- High strength and hardness
- High thermal conductivity
- High electrical conductivity
- Very good EMI/ RFI isolation
- Good processing properties
- Aerospace
- Domestic Appliances
- Furniture
- Power Tools
- Electronics
- Machinery
- Lighting Technology
:quality(80)/images.vogel.de/vogelonline/bdb/1506300/1506374/original.jpg)
La fundición en cámara fría es el proceso más popular en la producción en masa de piezas de fundición de metales ligeros. Lea ahora los factores clave para la realización de un concepto de diseño ligero de coste reducido.
Materiales1
En la fundición a presión, se utilizan metales no ferrosos para fabricar componentes, y la elección de la aleación para una aplicación concreta depende del presupuesto, el peso y las propiedades del material.
El aluminio es uno de los materiales más importantes, con una cuota superior al 80 %, seguido del zinc y el magnesio. However, copper, lead and tin can also be used. The alloys have different properties. For example, aluminum (600°C) and magnesium (520°C) have a high melting point, zinc (380°C) and lead (320°C) a low melting point.
Die casting alloys offer many advantages:
:quality(80)/images.vogel.de/vogelonline/bdb/1317600/1317687/original.jpg)
Low-Pressure vs. High-Pressure Die Casting
Various processes are used in foundry practice. Castings can also be produced without high pressure. In the sand casting process, for example, the alloy is poured into a mold made of sand, which must be destroyed in order to reveal the manufactured component (lost foam). En la fundición a la cera perdida, que se utiliza para fabricar piezas de fundición muy pequeñas, los moldes y modelos (normalmente de cera o plástico) también se destruyen tras el proceso de fundición. Otro ejemplo es la fundición por gravedad, que utiliza un molde metálico permanente pero no utiliza alta presión para presionar la masa fundida en el molde. Más bien, la fundición se fabrica o el molde se llena por gravedad.
También hay diferencias en el proceso de fundición a presión. Por ejemplo, hay procesos que utilizan alta o baja presión para producir los componentes. Mientras que la fundición a presión de alta presión representa alrededor del 50 % de la producción de fundición de metales ligeros, la fundición a presión de baja presión solo representa algo menos del 20 % de la producción total.2
La fundición a presión de baja presión utiliza principalmente aleaciones con puntos de fusión bajos. Es posible fundir componentes de 2 a 150 kg. Las ventajas son que se pueden alcanzar valores de resistencia muy elevados y geometrías complejas, así como un mejor aprovechamiento del material y una mayor precisión dimensional. El proceso es menos adecuado para piezas de paredes muy finas, ya que sólo puede obtenerse un espesor de pared mínimo de 3 mm. También hay que mencionar que los ciclos de fundición utilizando la fundición a baja presión son más lentos que los de alta presión.
En la fundición a alta presión, la masa fundida se presiona en el molde a alta presión y a gran velocidad, acelerando así el ciclo de fundición. Además, se pueden producir piezas fundidas de paredes más finas (con un grosor de pared mínimo de 1 mm) con superficies más lisas. La desventaja de este proceso de fabricación, sin embargo, es que se incurre en altos costos de operación y de inversión, los valores de resistencia son más bajos y el peso de la fundición a presión es limitado porque depende de la fuerza de cierre de la máquina.
:quality(80)/images.vogel.de/vogelonline/bdb/1508700/1508781/original.jpg)
Campos de aplicación
La fundición a presión se utiliza principalmente para la producción de grandes series, es decir, para fundir muchos componentes del mismo tipo. Despite the high pressure used during the manufacturing process, a high casting quality is achieved. The die casting process is particularly suitable for the production of very thin (up to 1 mm) (lightweight) components.
Most commonly, die cast components are manufactured for the automotive industry, such as wheels, blocks, cylinder heads, valve blocks and manifolds. This sector accounts for around 84 % of the castings produced by German foundries. 3 The use of aluminum parts leads to a reduction in the weight of the vehicles and thus to a reduction in fuel consumption. In addition, there are other industries in which die cast parts are used:
In the future, other industries such as electromobility will be of interest to foundries. Esto ofrece un enorme potencial para las fundiciones de metales ligeros.4
Historia de las fundiciones a presión 5
La fundición a presión surgió a mediados del siglo XIX, cuando floreció la industria editorial. El objetivo era poder imprimir periódicos y libros de forma rápida, flexible y económica. Para ello, se creó un dispositivo manual en el que se podía fundir una aleación de estaño y plomo para formar las letras (1838), la imprenta rotativa (1846) y, finalmente, la máquina tipográfica Linotype (1886). Uno de los principales elementos de esta máquina era una máquina de fundición integrada que vertía plomo líquido en los moldes de las letras de latón. Tras la fundición, las matrices volvían al almacén de matrices y las líneas de plomo fundidas eran expulsadas. A continuación, las líneas de plomo se ensamblaban en páginas que servían como planchas de impresión para la impresión en hojas o como plantillas para las planchas de impresión redondas necesarias para el proceso de impresión rotativa.
:quality(80)/images.vogel.de/vogelonline/bdb/1475800/1475868/original.jpg)
Durante los primeros 30 años, la fundición a presión se utilizó prácticamente de forma exclusiva en la industria de la impresión. El punto de inflexión se produjo cuando Herman H. Doehler fundó en 1908 la Doehler die casting Company, que a principios de la década de 1940 estaba considerada como el mayor fabricante de piezas de fundición a presión del mundo y que existió hasta 1998. La primera máquina de fundición a presión disponible en el mercado, que contenía todos los componentes esenciales de una máquina de fundición a presión moderna, fue desarrollada en 1925 por Joseph Soss y Louis H. Morin en los Estados Unidos.
Durante los últimos años del siglo XIX y las primeras décadas del siglo XX, aparecieron nuevos productos en el mercado y la producción industrial creció rápidamente. Los fabricantes reconocieron las ventajas de la fundición a presión, que podía utilizarse para producir de forma económica piezas para máquinas de escribir, cajas registradoras, relojes y aparatos eléctricos. Los fabricantes de juguetes también utilizaron la fundición a presión para producir coches de juguete y maquetas lo más fieles posible al original. Por último, pero no por ello menos importante, la emergente industria del automóvil y sus proveedores se convirtieron en importantes compradores de productos de fundición a presión.
Desde principios del siglo XX, la tecnología de la fundición a presión ha progresado con creciente rapidez. Al principio, el plomo y el estaño, dos metales con una temperatura de fusión relativamente baja y una buena ductilidad, se utilizaban principalmente en la fundición a presión. Hacia 1914 se empezó a trabajar con aleaciones de zinc y aluminio, que ofrecían mayor resistencia. En la década de 1930 se añadieron las aleaciones de cobre y magnesio. El magnesio, que con una densidad específica de 1,74 g/cm3 pesa un tercio menos que el metal ligero aluminio (2,75 g/cm3) y se utiliza hoy principalmente en la industria del automóvil, experimentó su primer auge como material de fundición a presión entre 1946 y 1978: El motor y la caja de cambios del VW Beetle se fabricaron con este material. Sin embargo, la tecnología de fundición a presión no se quedó en este nivel de desarrollo. Las máquinas se equiparon con una refinada tecnología de control y se hicieron cada vez más potentes. Los aceros para herramientas con propiedades mejoradas llegaron al mercado para la fabricación de moldes, y las propiedades físicas de las aleaciones de fundición a presión se optimizaron, de modo que hoy en día se pueden producir piezas de fundición con espesores de pared muy finos y con altas propiedades mecánicas. Los temas actuales incluyen la automatización, la eficiencia energética y de las materias primas, las formas complejas, las piezas híbridas, la automatización de los procesos y la digitalización (Industria 4.0).
:quality(80)/images.vogel.de/vogelonline/bdb/1518000/1518051/original.jpg)
1) Dynacast, metales fundidos a presión, disponible en https://www.dynacast.de/druckgussmetalle-al-mg-zn
2) La fundición de metales, disponible en http://www.themetalcasting.com/pressure-die-casting.html
3) BD Guss, 2016
4) NürnbergMesse, 2018, disponible en https://www.euroguss.de/de/news/presseinformationen/zukunft-von-druckguss-7sxvrxjjb7_pireport
5) NürnbergMesse, 2018, available on https://www.euroguss.de/de/news/fachartikel/fachartikel-druckgiessen-nl2jm1fcex_pireport
Further References
KUG BD Guss, 2009, Die Casting – Series production for highly complex thin-walled light metal castings, available on https://www.kug.bdguss.de/giessverfahren-inhalte/druckguss/
Powerguss – Haus der Gießerei-Industrie, Die casting – how does it work?, available on https://www.powerguss.de/was-ist-giessen/druckguss/
Lechuga, G., 2016, Die Casting Facts Infographic, available on https://www.slideshare.net/GermnLechuga/die-casting-facts-infographic
Dynacast, die casting, available on https://www.dynacast.de/druckguss