Az alapismeretek
Mi az a szerszámöntés és hogyan fejlődött a 19. század óta? Ezt és sok más alapismeretet, például a különböző eljárások és anyagok használatát ismertetjük a következő cikkben.
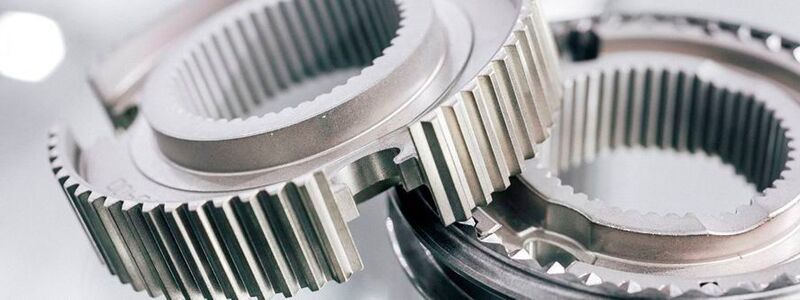
A szerszámöntés az egyik leggazdaságosabb és leggyorsabb formázási eljárás. Ennek a gyártási eljárásnak az az előnye, hogy egyetlen szerszámmal viszonylag gyorsan több százezer öntvényt lehet előállítani. Minden előállított alkatrész egységes minőségű és viszonylag alacsony fajlagos költséggel jár. De hogyan is néz ki pontosan a gyártási folyamat? Milyen anyagokat lehet felhasználni, és milyen területeken használják fel az öntvényeket?
A “szerszámöntés”
A szerszámöntés egy automatizált öntési eljárás, amelyben a folyékony olvadékot nagy nyomás (150-1200 bar) és nagy töltési sebesség (akár 540 km/h) mellett préselik egy formába. Általában alacsony olvadáspontú ötvözeteket használnak. Ez az öntési eljárás különösen alkalmas alkatrészek sorozat- és tömeggyártására, mivel – például a homoköntéssel ellentétben – állandó fémformákat használnak, amelyeket az öntés után nem kell megsemmisíteni. Lehetőség van nagyméretű és összetett alkatrészek gyártására alacsony falvastagsággal.
#expert
:quality(80)/images.vogel.de/vogelonline/bdb/1420000/1420060/original.jpg)
Szerszámok
A kiváló minőségű, hőálló acélfajtákból készült öntőformák két félből állnak, amelyek egy üreget alkotnak, amelybe a folyékony olvadékot az öntési folyamat során belenyomják. A felületek egy rögzített és egy mozgatható géplemezen helyezkednek el. Az öntési folyamat során nagy nyomás éri az öntőforma feleket, ezért a szerszámot reteszekkel látják el. Ezenkívül az öntőforma bizonyos részeit hűtik és/vagy melegítik, hogy az öntvény a kívánt módon megszilárduljon. A formák előállítása nagyon drága és időigényes, de egyetlen öntőformával több tízezer és több mint egymillió öntvény is előállítható. Az újrafelhasználható öntőformák további előnye, hogy az olvadék gyorsan lehűl.
Funkció és eljárások
A fröccsöntésben az alkatrészek gyártásának kétféle módja van: a melegkamrás és a hidegkamrás fröccsöntés. Mindkét gyártási eljárásnál a formát az öntési folyamat előtt egy leválasztószerrel permetezik be annak érdekében, hogy a később öntött alkatrész könnyen kivehető legyen a formából. Az olvadékot azonban nem közvetlenül a forma üregébe öntik, hanem először a nyomásos öntőgép öntőkamrájába töltik. Onnan az ötvözetet egy vagy több csatornán keresztül egy dugattyú (az ún. öntőkészlet) préseli a formába. A két eljárás közötti különbség az alábbiakban ismertetett öntőkamra felépítésében rejlik.
Melegkamrás öntési eljárás
A melegkamrás öntőgépek jellemzője, hogy az öntőkamra folyamatosan érintkezik a folyékony ötvözettel. Az olvadék egy szelepen keresztül jut az öntőkamrába, ahol a dugattyú nagy sebességgel a zárt öntőformába nyomja. Ezt az eljárást alacsony olvadáspontú ötvözetek, például cink, ólom vagy ón esetében alkalmazzák.
Hidegkamrás öntési módszer
A hidegkamrás öntőgépeket úgy tervezik, hogy az öntőkészlet az olvadékon kívül helyezkedik el. Az alkatrész előállításához az ötvözetet az öntőkamrába töltik, és csatornákon keresztül a szerszámöntőformába nyomják. Ez az eljárás magasabb olvadáspontú anyagokhoz alkalmas. Ezek közé tartozik például az alumínium és a réz.
Az ötvözet öntőformába való préselése után mindkét eljárásnál az alkatrész az erős nyomás hatására megszilárdul, mire az öntőforma reteszeit ki lehet nyitni. A kapuval ellátott alkatrészt automatikusan működtetett kilökőcsapok távolítják el a szerszámból, és szükség esetén tovább lehet dolgozni. Egyszerűen fogalmazva, az öntési folyamat a következő lépésekre osztható, és a gyakorlatban százmásodpercek – vagy akár csak ezredmásodpercek – alatt zajlik:
- Az öntőforma gyors feltöltése az ötvözettel
- Az alkatrész kikeményítése nagy nyomás alatt
- A forma kinyitása és az alkatrész eltávolítása
:quality(80)/images.vogel.de/vogelonline/bdb/1506300/1506374/original.jpg)
A hidegkamrás öntés a legnépszerűbb eljárás a könnyűfémöntvények tömeggyártásában. Olvasson most a költségcsökkentett könnyűszerkezetes tervezési koncepció megvalósításának kulcstényezőiről.
Az anyagok1
A nyomásos öntés során színesfémeket használnak az alkatrészek gyártásához, és az adott alkalmazáshoz szükséges ötvözet kiválasztása a költségvetéstől, a tömegtől és az anyagtulajdonságoktól függ.
Az alumínium az egyik legfontosabb anyag több mint 80 %-os részesedéssel, amelyet a cink és a magnézium követ. However, copper, lead and tin can also be used. The alloys have different properties. For example, aluminum (600°C) and magnesium (520°C) have a high melting point, zinc (380°C) and lead (320°C) a low melting point.
Die casting alloys offer many advantages:
- High corrosion resistance
- High strength and hardness
- High thermal conductivity
- High electrical conductivity
- Very good EMI/ RFI isolation
- Good processing properties
:quality(80)/images.vogel.de/vogelonline/bdb/1317600/1317687/original.jpg)
Low-Pressure vs. High-Pressure Die Casting
Various processes are used in foundry practice. Castings can also be produced without high pressure. In the sand casting process, for example, the alloy is poured into a mold made of sand, which must be destroyed in order to reveal the manufactured component (lost foam). A nagyon kis méretű öntött alkatrészek gyártására használt öntésnél a (rendszerint viaszból vagy műanyagból készült) öntőformákat és modelleket az öntési folyamat után szintén megsemmisítik. Egy másik példa a gravitációs öntés, amely állandó fémformát használ, de nem használ nagy nyomást az olvadéknak a formába való préseléséhez. Inkább az öntvényt a gravitáció segítségével állítják elő, illetve töltik meg a formát.
A szerszámöntési folyamatban is vannak különbségek. Például vannak olyan eljárások, amelyek vagy magas vagy alacsony nyomást használnak az alkatrészek előállításához. Míg a nagynyomású öntés a könnyűfémöntés termelésének mintegy 50 %-át teszi ki, addig az alacsonynyomású öntés a teljes termelésnek csak alig 20 %-át teszi ki.2
Az alacsonynyomású öntés elsősorban alacsony olvadáspontú ötvözeteket használ. Lehetőség van 2 és 150 kg közötti alkatrészek öntésére. Előnye, hogy nagyon magas szilárdsági értékek és összetett geometriák, valamint jobb anyagkihasználás és méretpontosság érhető el. Az eljárás kevésbé alkalmas nagyon vékony falú alkatrészekhez, mivel csak legalább 3 mm-es falvastagság érhető el. Azt is meg kell említeni, hogy a kisnyomású öntéssel végzett öntési ciklusok lassabbak, mint a nagynyomásúak.
A nagynyomású öntésnél az olvadékot nagy nyomáson és nagy sebességgel préselik a formába, így az öntési ciklus felgyorsul. Ezenkívül vékonyabb falú (legalább 1 mm falvastagságú), simább felületű öntvények állíthatók elő. Ennek a gyártási eljárásnak azonban hátránya, hogy magas üzemeltetési és beruházási költségek merülnek fel, a szilárdsági értékek alacsonyabbak, és az öntvény tömege korlátozott, mivel a gép záróerejétől függ.
:quality(80)/images.vogel.de/vogelonline/bdb/1508700/1508781/original.jpg)
Alkalmazási területek
A szerszámöntést elsősorban nagy sorozatgyártásra használják, azaz sok azonos típusú alkatrészt kell önteni. Despite the high pressure used during the manufacturing process, a high casting quality is achieved. The die casting process is particularly suitable for the production of very thin (up to 1 mm) (lightweight) components.
Most commonly, die cast components are manufactured for the automotive industry, such as wheels, blocks, cylinder heads, valve blocks and manifolds. This sector accounts for around 84 % of the castings produced by German foundries. 3 The use of aluminum parts leads to a reduction in the weight of the vehicles and thus to a reduction in fuel consumption. In addition, there are other industries in which die cast parts are used:
- Aerospace
- Domestic Appliances
- Furniture
- Power Tools
- Electronics
- Machinery
- Lighting Technology
In the future, other industries such as electromobility will be of interest to foundries. Ez óriási lehetőségeket kínál a könnyűfémöntvények számára.4
A szerszámöntés története 5
A szerszámöntés a 19. század közepén jött létre, amikor a könyvkiadás virágzott. A cél az volt, hogy gyorsan, rugalmasan és költséghatékonyan lehessen újságokat és könyveket nyomtatni. Ezek közé tartozik a kézzel működtetett berendezés, amelyben ón és ólom ötvözetéből betűket lehetett önteni (1838), a rotációs nyomdagép (1846) és végül a Linotype szedőgép (1886). Ennek a gépnek az egyik fő eleme egy beépített öntőgép volt, amely folyékony ólmot öntött a sárgaréz betűszerszámokból készült vonalas formákba. Az öntés után a mátrixokat visszatették a mátrixraktárba, és az öntött ólomsorokat kilökték. Az ólomvonalakat ezután lapokká állították össze, amelyek nyomólemezként szolgáltak az íves nyomtatáshoz, illetve sablonként a rotációs nyomtatáshoz szükséges kerek nyomólemezekhez.
:quality(80)/images.vogel.de/vogelonline/bdb/1475800/1475868/original.jpg)
Az első 30 évben a nyomdaiparban gyakorlatilag kizárólag a nyomdaipari öntést alkalmazták. A fordulópontot az jelentette, amikor Herman H. Doehler 1908-ban megalapította a Doehler nyomóöntő vállalatot, amely az 1940-es évek elején a világ legnagyobb nyomóöntvény alkatrészgyártójának számított, és 1998-ig létezett. A piacon kapható első nyomóöntőgépet, amely tartalmazta a modern nyomóöntőgépek minden lényeges alkatrészét, 1925-ben Joseph Soss és Louis H. Morin fejlesztette ki az Egyesült Államokban.
A 19. század végén és a 20. század első évtizedeiben új termékek jelentek meg a piacon, és az ipari termelés gyorsan nőtt. A gyártók felismerték a fröccsöntés előnyeit, amellyel gazdaságosan lehetett alkatrészeket gyártani írógépekhez, pénztárgépekhez, órákhoz és elektromos készülékekhez. A játékgyártók a lehető leghűbb játék- és modellautók gyártására is használták a fröccsöntést. Végül, de nem utolsósorban a feltörekvő autóipar és annak beszállítói a nyomásos öntvénytermékek fontos vásárlóivá váltak.
A 20. század eleje óta a nyomásos öntési technológia egyre gyorsabban fejlődött. Kezdetben főként ólmot és ónt, két viszonylag alacsony olvadási hőmérsékletű és jó alakíthatóságú fémet használtak a nyomóöntéshez. 1914 körül kezdtek el dolgozni a cink- és alumíniumötvözeteken, amelyek nagyobb szilárdságot kínáltak. Az 1930-as években réz- és magnéziumötvözetek is megjelentek. A magnézium, amely 1,74 g/cm3 fajlagos sűrűségével egyharmaddal kevesebbet nyom, mint a könnyűfém alumínium (2,75 g/cm3), és amelyet ma főként az autóiparban használnak, 1946 és 1978 között élte meg első fellendülését mint öntőanyag: A VW Bogár motorja és sebességváltója ebből az anyagból készült. A szerszámöntési technológia azonban nem maradt meg ezen a fejlődési szinten. A gépeket kifinomult vezérléstechnikával látták el, és egyre nagyobb teljesítményűvé váltak. Jobb tulajdonságokkal rendelkező szerszámacélok jelentek meg a piacon a formakészítéshez, és optimalizálták a szerszámöntő ötvözetek fizikai tulajdonságait, így ma már nagyon vékony falvastagságú és nagy mechanikai tulajdonságokkal rendelkező öntött alkatrészek is előállíthatók. Az aktuális témák közé tartozik az automatizálás, az energia- és nyersanyaghatékonyság, az összetett formák, a hibrid alkatrészek, a folyamatautomatizálás és a digitalizáció (Ipar 4.0).
:quality(80)/images.vogel.de/vogelonline/bdb/1518000/1518051/original.jpg)
1) Dynacast, öntött fémek, elérhető a https://www.dynacast.de/druckgussmetalle-al-mg-zn
2) A fémöntés, elérhető a http://www.themetalcasting.com/pressure-die-casting.html
3) BD Guss, 2016
4) NürnbergMesse, 2018, elérhető a https://www.euroguss.de/de/news/presseinformationen/zukunft-von-druckguss-7sxvrxjjb7_pireport
5) NürnbergMesse, 2018, available on https://www.euroguss.de/de/news/fachartikel/fachartikel-druckgiessen-nl2jm1fcex_pireport
Further References
KUG BD Guss, 2009, Die Casting – Series production for highly complex thin-walled light metal castings, available on https://www.kug.bdguss.de/giessverfahren-inhalte/druckguss/
Powerguss – Haus der Gießerei-Industrie, Die casting – how does it work?, available on https://www.powerguss.de/was-ist-giessen/druckguss/
Lechuga, G., 2016, Die Casting Facts Infographic, available on https://www.slideshare.net/GermnLechuga/die-casting-facts-infographic
Dynacast, die casting, available on https://www.dynacast.de/druckguss