Wiedza podstawowa
Czym jest odlewanie ciśnieniowe i jak przebiegał jego rozwój od XIX wieku? To i wiele innych podstaw, takich jak wykorzystanie różnych procesów i materiałów, wyjaśniono w poniższym artykule.
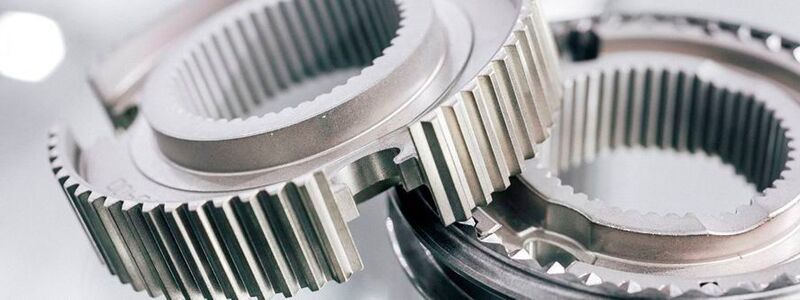
Odlewanie pod ciśnieniem jest jednym z najbardziej ekonomicznych i najszybszych procesów formowania. Zaletą tego procesu produkcyjnego jest to, że setki tysięcy odlewów mogą być produkowane stosunkowo szybko przy użyciu tylko jednej formy. Wszystkie produkowane elementy mają jednolitą jakość i wiążą się z relatywnie niskimi kosztami jednostkowymi. Ale jak dokładnie wygląda proces produkcyjny? Jakie materiały mogą być użyte i w jakich obszarach są stosowane odlewy?
Definicja „Odlewanie kokilowe”
Odlewanie kokilowe jest zautomatyzowanym procesem odlewania, w którym płynny stop jest wtłaczany do formy pod wysokim ciśnieniem (150 do 1200 bar) i z dużą prędkością napełniania (do 540 km/h). Zazwyczaj stosowane są stopy o niskiej temperaturze topnienia. Ten proces odlewania nadaje się szczególnie do seryjnej i masowej produkcji elementów, ponieważ w przeciwieństwie np. do odlewania w piasku, stosowane są trwałe formy metalowe, które nie muszą być niszczone po odlaniu. Możliwa jest produkcja dużych i złożonych komponentów o niewielkiej grubości ścianek.
#expert
:quality(80)/images.vogel.de/vogelonline/bdb/1420000/1420060/original.jpg)
Formy
Formy odlewnicze, wykonane z wysokiej jakości gatunków stali żaroodpornej, składają się z dwóch połówek tworzących wnękę, do której podczas procesu odlewania wtłaczany jest płynny stop. Połówki są umieszczone na stałej i ruchomej płycie maszyny. Podczas procesu odlewania na połówki formy wywierany jest duży nacisk, dlatego też forma wyposażona jest w zatrzaski. Dodatkowo, niektóre części formy są chłodzone i/lub podgrzewane, aby odlew zastygł w pożądany sposób. Produkcja form jest bardzo kosztowna i czasochłonna, ale za pomocą jednej z nich można wykonać od kilkudziesięciu tysięcy do ponad miliona odlewów. Kolejną zaletą form odlewniczych wielokrotnego użytku jest to, że stopiony materiał szybko stygnie.
Funkcjonalność i procedury
W odlewaniu ciśnieniowym, istnieją dwa różne sposoby wytwarzania komponentów: odlewanie z gorącą komorą i odlewanie z zimną komorą. W obu procesach produkcyjnych, forma jest spryskiwana środkiem oddzielającym przed procesem odlewania, aby zapewnić, że odlana część może być łatwo wyjęta z formy. Stopiony materiał nie jest jednak wlewany bezpośrednio do wnęki formy, lecz jest najpierw wlewany do komory odlewniczej maszyny do odlewania ciśnieniowego. Stamtąd stop jest wciskany do formy przez tłok (tzw. zestaw odlewniczy) przez jeden lub więcej kanałów. Różnica pomiędzy tymi dwoma procesami leży w strukturze komory odlewniczej, jak opisano poniżej.
Metoda odlewania kokilowego z gorącą komorą
Charakterystyczną cechą maszyn odlewniczych z gorącą komorą jest to, że komora odlewnicza jest w stałym kontakcie z ciekłym stopem. Roztopiony stop przechodzi przez zawór do komory odlewniczej, gdzie jest wtłaczany z dużą prędkością do zamkniętej formy odlewniczej przez tłok. Proces ten jest stosowany do stopów o niskiej temperaturze topnienia, takich jak cynk, ołów lub cyna.
Metoda odlewania w zimnej komorze
Maszyny odlewnicze z zimną komorą są zaprojektowane w taki sposób, że zestaw odlewniczy znajduje się poza topnikiem. Aby wyprodukować komponent, stop jest napełniany do komory odlewniczej i wciskany do formy odlewniczej przez kanały. Proces ten jest odpowiedni dla materiałów o wyższej temperaturze topnienia. Należą do nich np. aluminium i miedź.
Po wciśnięciu stopu do formy w obu procesach, komponent krzepnie pod silnym ciśnieniem, po czym można otworzyć zatrzaski formy. Część z wrotami jest wyjmowana z formy przez automatycznie działające trzpienie wyrzutowe i w razie potrzeby może być poddana dalszej obróbce. Najprościej rzecz ujmując, proces odlewania można podzielić na następujące etapy i w praktyce przebiega on w setnych częściach sekundy – lub nawet tylko w tysięcznych częściach sekundy:
- Szybkie wypełnienie formy odlewniczej stopem
- Utwardzanie komponentu pod wysokim ciśnieniem
- Otwarcie formy i usunięcie komponentu
:quality(80)/images.vogel.de/vogelonline/bdb/1506300/1506374/original.jpg)
Odlewanie kokilowe w zimnej komorze jest najpopularniejszym procesem w masowej produkcji odlewów z metali lekkich. Przeczytaj teraz o kluczowych czynnikach dla realizacji koncepcji lekkiej konstrukcji o zredukowanych kosztach.
Materiały1
W odlewaniu ciśnieniowym, metale nieżelazne są wykorzystywane do produkcji komponentów, a wybór stopu dla konkretnego zastosowania zależy od budżetu, wagi i właściwości materiału.
Aluminium jest jednym z najważniejszych materiałów z udziałem ponad 80 %, a następnie cynk i magnez. However, copper, lead and tin can also be used. The alloys have different properties. For example, aluminum (600°C) and magnesium (520°C) have a high melting point, zinc (380°C) and lead (320°C) a low melting point.
Die casting alloys offer many advantages:
- High corrosion resistance
- High strength and hardness
- High thermal conductivity
- High electrical conductivity
- Very good EMI/ RFI isolation
- Good processing properties
:quality(80)/images.vogel.de/vogelonline/bdb/1317600/1317687/original.jpg)
Low-Pressure vs. High-Pressure Die Casting
Various processes are used in foundry practice. Castings can also be produced without high pressure. In the sand casting process, for example, the alloy is poured into a mold made of sand, which must be destroyed in order to reveal the manufactured component (lost foam). W odlewnictwie inwestycyjnym, które jest stosowane do produkcji bardzo małych elementów odlewanych, formy i modele (zwykle wykonane z wosku lub tworzywa sztucznego) są również niszczone po procesie odlewania. Innym przykładem jest odlewanie grawitacyjne, w którym używa się stałej formy metalowej, ale nie stosuje się wysokiego ciśnienia do wciskania stopionego materiału do formy. Raczej, odlew jest produkowany lub forma wypełniana przez grawitację.
Istnieją również różnice w procesach odlewania ciśnieniowego. Na przykład, istnieją procesy, które wykorzystują wysokie lub niskie ciśnienie do produkcji komponentów. Podczas gdy odlewanie wysokociśnieniowe stanowi około 50 % produkcji odlewów metali lekkich, odlewanie niskociśnieniowe stanowi tylko niecałe 20 % całkowitej produkcji.2
Do odlewania niskociśnieniowego używa się przede wszystkim stopów o niskich temperaturach topnienia. Możliwe jest odlewanie elementów o wadze od 2 do 150 kg. Zaletami są bardzo wysokie wartości wytrzymałości i złożone geometrie, jak również lepsze wykorzystanie materiału i dokładność wymiarowa. Proces ten jest mniej odpowiedni dla bardzo cienkościennych części, ponieważ można uzyskać tylko minimalną grubość ścianki 3 mm. Należy również wspomnieć, że cykle odlewania z zastosowaniem odlewania pod niskim ciśnieniem są wolniejsze niż pod wysokim ciśnieniem.
W odlewaniu pod wysokim ciśnieniem, stopiony materiał jest wtłaczany do formy pod wysokim ciśnieniem i z dużą prędkością, co przyspiesza cykl odlewania. Ponadto, można produkować odlewy o cieńszych ściankach (minimalna grubość ścianki 1 mm) i gładszych powierzchniach. Wadą tego procesu produkcyjnego jest jednak to, że ponoszone są wysokie koszty operacyjne i inwestycyjne, wartości wytrzymałości są niższe, a masa odlewu ciśnieniowego jest ograniczona, ponieważ zależy od siły zamykania maszyny.
:quality(80)/images.vogel.de/vogelonline/bdb/1508700/1508781/original.jpg)
Pole zastosowania
Odlewanie matrycowe jest stosowane głównie do produkcji wielkoseryjnej, tzn. do odlewania wielu elementów tego samego typu. Despite the high pressure used during the manufacturing process, a high casting quality is achieved. The die casting process is particularly suitable for the production of very thin (up to 1 mm) (lightweight) components.
Most commonly, die cast components are manufactured for the automotive industry, such as wheels, blocks, cylinder heads, valve blocks and manifolds. This sector accounts for around 84 % of the castings produced by German foundries. 3 The use of aluminum parts leads to a reduction in the weight of the vehicles and thus to a reduction in fuel consumption. In addition, there are other industries in which die cast parts are used:
- Aerospace
- Domestic Appliances
- Furniture
- Power Tools
- Electronics
- Machinery
- Lighting Technology
In the future, other industries such as electromobility will be of interest to foundries. Daje to ogromny potencjał dla odlewów z metali lekkich.4
Historia odlewów ciśnieniowych 5
Odlewanie ciśnieniowe powstało w połowie XIX wieku, kiedy to nastąpił rozkwit wydawnictw. Celem było umożliwienie szybkiego, elastycznego i ekonomicznego drukowania gazet i książek. Powstało wtedy ręczne urządzenie do odlewania liter ze stopu cyny i ołowiu (1838), rotacyjna prasa drukarska (1846) i wreszcie maszyna do składu drukarskiego Linotype (1886). Jednym z głównych elementów tej maszyny była zintegrowana maszyna odlewnicza, która wlewała ciekły ołów do form liniowych wykonanych z mosiężnych matryc literniczych. Po odlaniu matryce wracały do magazynu matryc, a odlane ołowiane linie były wyrzucane. Linie ołowiane były następnie łączone w strony, które służyły jako płyty drukarskie dla druku arkuszowego lub jako szablony dla okrągłych płyt drukarskich wymaganych w procesie druku rotacyjnego.
:quality(80)/images.vogel.de/vogelonline/bdb/1475800/1475868/original.jpg)
Przez pierwsze 30 lat, odlewanie ciśnieniowe było praktycznie wyłącznie stosowane w przemyśle drukarskim. Punktem zwrotnym było założenie przez Hermana H. Doehlera firmy Doehler Die Casting Company w 1908 roku, która na początku lat 40-tych była uważana za największego na świecie producenta części odlewanych ciśnieniowo i istniała do 1998 roku. Pierwsza dostępna na rynku maszyna do odlewania ciśnieniowego, która zawierała wszystkie istotne elementy nowoczesnej maszyny do odlewania ciśnieniowego, została skonstruowana w 1925 roku przez Josepha Sossa i Louisa H. Morina w USA.
Pod koniec XIX wieku i w pierwszych dekadach XX wieku na rynku pojawiały się nowe produkty, a produkcja przemysłowa szybko rosła. Producenci docenili zalety odlewania ciśnieniowego, które można było wykorzystać do ekonomicznej produkcji części do maszyn do pisania, kas fiskalnych, zegarków i urządzeń elektrycznych. Również producenci zabawek wykorzystywali odlewanie ciśnieniowe do produkcji zabawek i modeli samochodów, które były jak najbardziej wierne oryginałowi. Wreszcie, rozwijający się przemysł motoryzacyjny i jego dostawcy stali się ważnymi nabywcami produktów odlewanych ciśnieniowo.
Od początku XX wieku technologia odlewania ciśnieniowego postępowała z coraz większą prędkością. Początkowo, ołów i cyna, dwa metale o stosunkowo niskiej temperaturze topnienia i dobrej plastyczności, były głównie używane w odlewaniu ciśnieniowym. Około roku 1914 rozpoczęto prace nad stopami cynku i aluminium, które charakteryzowały się większą wytrzymałością. W latach trzydziestych dodano stopy miedzi i magnezu. Magnez, który przy gęstości właściwej 1,74 g/cm3 waży o jedną trzecią mniej niż lekki metal aluminium (2,75 g/cm3) i jest dziś stosowany głównie w przemyśle samochodowym, przeżywał swój pierwszy rozkwit jako materiał odlewniczy w latach 1946-1978: Silnik i skrzynia biegów w VW Beetle były wykonane z tego materiału. Jednak technologia odlewania ciśnieniowego nie zatrzymała się na tym poziomie rozwoju. Maszyny zostały wyposażone w udoskonaloną technikę sterowania i stawały się coraz bardziej wydajne. Na rynku pojawiły się stale narzędziowe o ulepszonych właściwościach do produkcji form, a właściwości fizyczne stopów odlewniczych zostały zoptymalizowane tak, że dziś można produkować części odlewane o bardzo cienkich ściankach i wysokich właściwościach mechanicznych. Aktualne tematy obejmują automatyzację, efektywność energetyczną i surowcową, złożone kształty, części hybrydowe, automatyzację procesów i cyfryzację (Przemysł 4.0).
:quality(80)/images.vogel.de/vogelonline/bdb/1518000/1518051/original.jpg)
1) Dynacast, metale odlewane ciśnieniowo, dostępne na https://www.dynacast.de/druckgussmetalle-al-mg-zn
2) The Metal Casting, dostępny na http://www.themetalcasting.com/pressure-die-casting.html
3) BD Guss, 2016
4) NürnbergMesse, 2018, dostępny na https://www.euroguss.de/de/news/presseinformationen/zukunft-von-druckguss-7sxvrxjjb7_pireport
5) NürnbergMesse, 2018, available on https://www.euroguss.de/de/news/fachartikel/fachartikel-druckgiessen-nl2jm1fcex_pireport
Further References
KUG BD Guss, 2009, Die Casting – Series production for highly complex thin-walled light metal castings, available on https://www.kug.bdguss.de/giessverfahren-inhalte/druckguss/
Powerguss – Haus der Gießerei-Industrie, Die casting – how does it work?, available on https://www.powerguss.de/was-ist-giessen/druckguss/
Lechuga, G., 2016, Die Casting Facts Infographic, available on https://www.slideshare.net/GermnLechuga/die-casting-facts-infographic
Dynacast, die casting, available on https://www.dynacast.de/druckguss