Grundlagenwissen
Was ist Druckguss und wie hat er sich seit dem 19. Jahrhundert entwickelt? Dies und viele weitere Grundlagen wie die Verwendung verschiedener Verfahren und Materialien werden im folgenden Artikel erklärt.
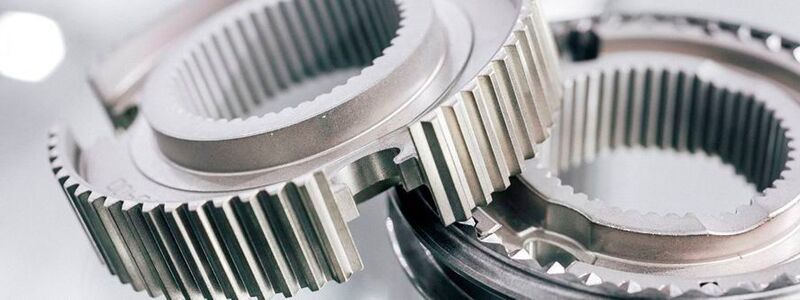
Das Druckgießen ist eines der wirtschaftlichsten und schnellsten Umformverfahren. Die Vorteile dieses Produktionsverfahrens liegen darin, dass mit nur einer Form relativ schnell hunderttausende von Gussteilen hergestellt werden können. Alle hergestellten Teile haben eine einheitliche Qualität und verursachen relativ geringe Stückkosten. Doch wie genau sieht der Herstellungsprozess aus? Welche Werkstoffe können verwendet werden und in welchen Bereichen werden die Gussteile eingesetzt?
Definition „Druckguss“
Der Druckguss ist ein automatisiertes Gießverfahren, bei dem die flüssige Schmelze unter hohem Druck (150 bis 1200 bar) und mit hoher Füllgeschwindigkeit (bis zu 540 km/h) in eine Form gepresst wird. In der Regel werden Legierungen mit einem niedrigen Schmelzpunkt verwendet. Dieses Gießverfahren eignet sich besonders gut für die Serien- und Massenproduktion von Bauteilen, da – anders als beispielsweise beim Sandguss – metallische Dauerformen verwendet werden, die nach dem Gießen nicht zerstört werden müssen. Es ist möglich, große und komplexe Bauteile mit geringen Wandstärken herzustellen.
#expert
:quality(80)/images.vogel.de/vogelonline/bdb/1420000/1420060/original.jpg)
Formen
Die Druckgussformen aus hochwertigen, hitzebeständigen Stahlsorten bestehen aus zwei Hälften, die einen Hohlraum bilden, in den die flüssige Schmelze während des Gießvorgangs gepresst wird. Die Hälften befinden sich auf einer festen und einer beweglichen Maschinenplatte. Während des Gießens wird ein hoher Druck auf die Formhälften ausgeübt, weshalb die Form mit Verriegelungen ausgestattet ist. Außerdem werden bestimmte Teile der Form gekühlt und/oder erwärmt, damit das Gussteil wie gewünscht erstarrt. Die Herstellung der Formen ist sehr teuer und zeitaufwendig, aber mit einer einzigen Form können mehrere zehntausend bis über eine Million Gussteile hergestellt werden. Ein weiterer Vorteil der wiederverwendbaren Gussformen ist, dass die Schmelze schnell abkühlt.
Funktionsweise und Verfahren
Im Druckguss gibt es zwei verschiedene Arten der Herstellung von Bauteilen: den Warmkammer- und den Kaltkammerdruckguss. Bei beiden Herstellungsverfahren wird die Form vor dem Gießvorgang mit einem Trennmittel besprüht, damit sich das spätere Gussteil leicht aus der Form lösen lässt. Allerdings wird die Schmelze nicht direkt in den Formhohlraum gegossen, sondern zunächst in die Gießkammer der Druckgießmaschine gefüllt. Von dort aus wird die Legierung durch einen Kolben (das so genannte Gießset) durch einen oder mehrere Kanäle in die Form gepresst. Der Unterschied zwischen den beiden Verfahren liegt im Aufbau der Gießkammer, der im Folgenden beschrieben wird.
Warmkammer-Druckgießverfahren
Charakteristisch für Warmkammer-Druckgießmaschinen ist, dass die Gießkammer ständig in Kontakt mit der flüssigen Legierung steht. Die Schmelze gelangt durch ein Ventil in die Gießkammer, wo sie mit hoher Geschwindigkeit durch den Kolben in die geschlossene Druckgussform gepresst wird. Dieses Verfahren wird für Legierungen mit niedrigem Schmelzpunkt, wie Zink, Blei oder Zinn, eingesetzt.
Kaltkammer-Druckgießverfahren
Kaltkammer-Druckgießmaschinen sind so konstruiert, dass sich das Gießgerät außerhalb der Schmelze befindet. Zur Herstellung eines Bauteils wird die Legierung in die Gießkammer gefüllt und durch Kanäle in die Druckgussform gepresst. Dieses Verfahren eignet sich für Werkstoffe mit einem höheren Schmelzpunkt. Dazu gehören zum Beispiel Aluminium und Kupfer.
Nachdem die Legierung bei beiden Verfahren in die Form gepresst wurde, erstarrt das Bauteil unter dem starken Druck, woraufhin die Verschlüsse der Form geöffnet werden können. Das Teil mit Anschnitt wird durch automatisch betätigte Auswerferstifte aus der Form entnommen und kann bei Bedarf weiterverarbeitet werden. Der Gießprozess lässt sich vereinfacht gesagt in folgende Schritte unterteilen und läuft in der Praxis in Hundertstel- oder sogar nur Tausendstelsekunden ab:
- Schnelle Befüllung der Gießform mit der Legierung
- Aushärtung des Bauteils unter hohem Druck
- Öffnen der Form und Entnahme des Bauteils
:quality(80)/images.vogel.de/vogelonline/bdb/1506300/1506374/original.jpg)
Kaltkammerdruckguss ist das beliebteste Verfahren in der Massenproduktion von Leichtmetallgussteilen. Lesen Sie jetzt über die Schlüsselfaktoren für die Realisierung eines kostenreduzierten Leichtbaukonzepts.
Werkstoffe1
Im Druckguss werden Nichteisenmetalle zur Herstellung von Bauteilen verwendet, und die Wahl der Legierung für eine bestimmte Anwendung hängt von Budget, Gewicht und Materialeigenschaften ab.
Aluminium ist mit einem Anteil von mehr als 80 % einer der wichtigsten Werkstoffe, gefolgt von Zink und Magnesium. However, copper, lead and tin can also be used. The alloys have different properties. For example, aluminum (600°C) and magnesium (520°C) have a high melting point, zinc (380°C) and lead (320°C) a low melting point.
Die casting alloys offer many advantages:
- High corrosion resistance
- High strength and hardness
- High thermal conductivity
- High electrical conductivity
- Very good EMI/ RFI isolation
- Good processing properties
:quality(80)/images.vogel.de/vogelonline/bdb/1317600/1317687/original.jpg)
Low-Pressure vs. High-Pressure Die Casting
Various processes are used in foundry practice. Castings can also be produced without high pressure. In the sand casting process, for example, the alloy is poured into a mold made of sand, which must be destroyed in order to reveal the manufactured component (lost foam). Beim Feinguss, der zur Herstellung sehr kleiner Gussteile verwendet wird, werden die Formen und Modelle (meist aus Wachs oder Kunststoff) nach dem Gießvorgang ebenfalls zerstört. Ein weiteres Beispiel ist das Kokillengießen, bei dem eine Dauerform aus Metall verwendet wird, die Schmelze aber nicht mit hohem Druck in die Form gepresst wird. Vielmehr wird das Gussteil durch die Schwerkraft hergestellt bzw. die Form gefüllt.
Auch beim Druckgussverfahren gibt es Unterschiede. So gibt es Verfahren, die entweder mit hohem oder mit niedrigem Druck arbeiten, um die Bauteile herzustellen. Während der Hochdruckdruckguss rund 50 % der Leichtmetallgussproduktion ausmacht, sind es beim Niederdruckguss nur knapp 20 %.2
Im Niederdruckguss werden vor allem Legierungen mit niedrigem Schmelzpunkt verwendet. Es ist möglich, Bauteile von 2 bis 150 kg zu gießen. Die Vorteile liegen darin, dass sehr hohe Festigkeitswerte und komplexe Geometrien sowie eine bessere Materialausnutzung und Maßhaltigkeit erreicht werden können. Für sehr dünnwandige Teile ist das Verfahren weniger geeignet, da nur eine Mindestwandstärke von 3 mm erreicht werden kann. Zu erwähnen ist auch, dass die Gießzyklen beim Niederdruckguss langsamer sind als beim Hochdruckguss.
Beim Hochdruckguss wird die Schmelze unter hohem Druck und mit hoher Geschwindigkeit in die Form gepresst, was den Gießzyklus beschleunigt. Außerdem können dünnwandigere Gussteile (Mindestwandstärke von 1 mm) mit glatteren Oberflächen hergestellt werden. Der Nachteil dieses Herstellungsverfahrens ist jedoch, dass hohe Betriebs- und Investitionskosten anfallen, die Festigkeitswerte geringer sind und das Druckgussgewicht begrenzt ist, da es von der Schließkraft der Maschine abhängt.
:quality(80)/images.vogel.de/vogelonline/bdb/1508700/1508781/original.jpg)
Anwendungsgebiete
Der Druckguss wird vor allem für die Großserienfertigung eingesetzt, d.h. wenn viele gleichartige Bauteile gegossen werden sollen. Despite the high pressure used during the manufacturing process, a high casting quality is achieved. The die casting process is particularly suitable for the production of very thin (up to 1 mm) (lightweight) components.
Most commonly, die cast components are manufactured for the automotive industry, such as wheels, blocks, cylinder heads, valve blocks and manifolds. This sector accounts for around 84 % of the castings produced by German foundries. 3 The use of aluminum parts leads to a reduction in the weight of the vehicles and thus to a reduction in fuel consumption. In addition, there are other industries in which die cast parts are used:
- Aerospace
- Domestic Appliances
- Furniture
- Power Tools
- Electronics
- Machinery
- Lighting Technology
In the future, other industries such as electromobility will be of interest to foundries. Dies bietet ein enormes Potenzial für den Leichtmetallguss.4
Geschichte des Druckgusses 5
Der Druckguss entstand Mitte des 19. Jahrhunderts, als das Verlagswesen aufblühte. Ziel war es, Zeitungen und Bücher schnell, flexibel und kostengünstig drucken zu können. Dazu gehörten ein handbetriebenes Gerät, in dem eine Legierung aus Zinn und Blei in Buchstaben gegossen werden konnte (1838), die Rotationsdruckmaschine (1846) und schließlich die Linotype-Setzmaschine (1886). Eines der Hauptelemente dieser Maschine war eine integrierte Druckgussmaschine, die flüssiges Blei in die aus Messingbuchstaben gefertigten Linienformen goss. Nach dem Gießen wurden die Matrizen in das Matrizenmagazin zurückgeführt und die gegossenen Bleizeilen ausgestoßen. Die Bleizeilen wurden dann zu Seiten zusammengesetzt, die als Druckplatten für den Bogendruck oder als Schablonen für die im Rotationsdruckverfahren benötigten runden Druckplatten dienten.
:quality(80)/images.vogel.de/vogelonline/bdb/1475800/1475868/original.jpg)
In den ersten 30 Jahren wurde der Druckguss praktisch ausschließlich in der Druckindustrie eingesetzt. Die Wende kam, als Herman H. Doehler 1908 die Doehler Druckgießerei gründete, die in den frühen 1940er Jahren als weltgrößter Hersteller von Druckgussteilen galt und bis 1998 existierte. Die erste auf dem Markt erhältliche Druckgussmaschine, die alle wesentlichen Komponenten einer modernen Druckgussmaschine enthielt, wurde 1925 von Joseph Soss und Louis H. Morin in den USA entwickelt.
Im späten 19. und in den ersten Jahrzehnten des 20. Jahrhunderts kamen neue Produkte auf den Markt und die industrielle Produktion wuchs rasant. Die Hersteller erkannten die Vorteile des Druckgusses, mit dem sich Teile für Schreibmaschinen, Registrierkassen, Uhren und Elektrogeräte wirtschaftlich herstellen ließen. Auch Spielzeughersteller nutzten den Druckguss, um möglichst originalgetreue Spielzeug- und Modellautos herzustellen. Nicht zuletzt wurden die aufstrebende Automobilindustrie und ihre Zulieferer zu wichtigen Abnehmern von Druckgussprodukten.
Seit dem frühen 20. Jahrhundert hat sich die Druckgusstechnologie immer schneller weiterentwickelt. Zunächst wurden vor allem Blei und Zinn, zwei Metalle mit relativ niedriger Schmelztemperatur und guter Duktilität, für den Druckguss verwendet. Um 1914 begann man mit der Arbeit an Zink- und Aluminiumlegierungen, die eine höhere Festigkeit aufwiesen. In den 1930er Jahren kamen Kupfer- und Magnesiumlegierungen hinzu. Magnesium, das mit einer spezifischen Dichte von 1,74 g/cm3 ein Drittel weniger wiegt als das Leichtmetall Aluminium (2,75 g/cm3) und heute vor allem in der Automobilindustrie eingesetzt wird, erlebte seinen ersten Boom als Druckgusswerkstoff zwischen 1946 und 1978: Motor und Getriebe des VW-Käfers wurden aus diesem Werkstoff gefertigt. Doch die Druckgusstechnik blieb nicht auf diesem Entwicklungsstand stehen. Die Maschinen wurden mit verfeinerter Steuerungstechnik ausgestattet und wurden immer leistungsfähiger. Für den Formenbau kamen Werkzeugstähle mit verbesserten Eigenschaften auf den Markt, und die physikalischen Eigenschaften der Druckgusslegierungen wurden optimiert, so dass heute Gussteile mit sehr dünnen Wandstärken und gleichzeitig hohen mechanischen Eigenschaften hergestellt werden können. Aktuelle Themen sind Automatisierung, Energie- und Rohstoffeffizienz, komplexe Formen, Hybridteile, Prozessautomatisierung und Digitalisierung (Industrie 4.0).
:quality(80)/images.vogel.de/vogelonline/bdb/1518000/1518051/original.jpg)
1) Dynacast, Metalldruckguss, erhältlich auf https://www.dynacast.de/druckgussmetalle-al-mg-zn
2) Der Metallguss, erhältlich auf http://www.themetalcasting.com/pressure-die-casting.html
3) BD Guss, 2016
4) NürnbergMesse, 2018, erhältlich auf https://www.euroguss.de/de/news/presseinformationen/zukunft-von-druckguss-7sxvrxjjb7_pireport
5) NürnbergMesse, 2018, available on https://www.euroguss.de/de/news/fachartikel/fachartikel-druckgiessen-nl2jm1fcex_pireport
Further References
KUG BD Guss, 2009, Die Casting – Series production for highly complex thin-walled light metal castings, available on https://www.kug.bdguss.de/giessverfahren-inhalte/druckguss/
Powerguss – Haus der Gießerei-Industrie, Die casting – how does it work?, available on https://www.powerguss.de/was-ist-giessen/druckguss/
Lechuga, G., 2016, Die Casting Facts Infographic, available on https://www.slideshare.net/GermnLechuga/die-casting-facts-infographic
Dynacast, die casting, available on https://www.dynacast.de/druckguss