Základní znalosti
Co je tlakové lití a jak se vyvíjelo od 19. století? To a mnoho dalších základních informací, jako je použití různých postupů a materiálů, se dozvíte v následujícím článku.
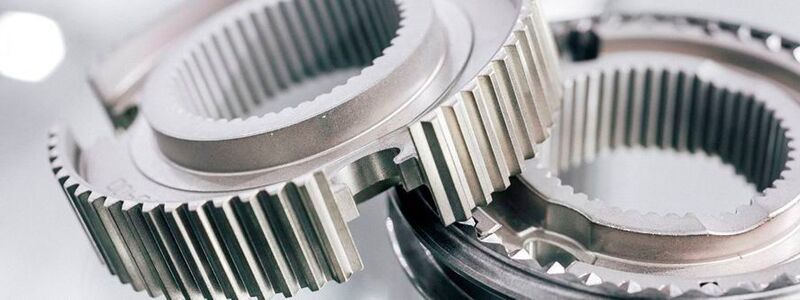
Lití pod tlakem je jedním z nejhospodárnějších a nejrychlejších procesů tváření. Výhody tohoto výrobního procesu spočívají v tom, že lze relativně rychle vyrobit statisíce odlitků za použití pouze jedné formy. Všechny vyrobené součásti mají jednotnou kvalitu a zahrnují relativně nízké jednotkové náklady. Jak ale přesně výrobní proces vypadá? Jaké materiály lze použít a v jakých oblastech se odlitky používají?
Definice pojmu „tlakové lití“
Tlakové lití je automatizovaný proces lití, při kterém se tekutá tavenina lisuje do formy pod vysokým tlakem (150 až 1200 barů) a při vysoké rychlosti plnění (až 540 km/h). Obvykle se používají slitiny s nízkou teplotou tání. Tento proces lití je vhodný zejména pro sériovou a hromadnou výrobu součástí, protože na rozdíl například od lití do písku se používají trvalé kovové formy, které se po odlití nemusí zničit. Je možné vyrábět velké a složité součásti s malou tloušťkou stěn.
#expert
:quality(80)/images.vogel.de/vogelonline/bdb/1420000/1420060/original.jpg)
Flísy
Flísy pro tlakové lití, vyrobené z vysoce kvalitních žáruvzdorných ocelí, se skládají ze dvou polovin, které tvoří dutinu, do níž je během procesu lití vtlačována tekutá tavenina. Poloviny jsou umístěny na pevné a pohyblivé desce stroje. Během procesu lití působí na poloviny formy vysoký tlak, a proto je forma vybavena západkami. Kromě toho se určité části formy chladí a/nebo zahřívají, aby odlitek podle potřeby ztuhl. Výroba forem je velmi nákladná a časově náročná, ale s jednou z nich lze vyrobit několik desítek tisíc až více než milion odlitků. Další výhodou opakovaně použitelných licích forem je, že tavenina rychle vychladne.
Funkčnost a postupy
Při tlakovém lití existují dva různé způsoby výroby součástí: tlakové lití s horkou komorou a tlakové lití se studenou komorou. Při obou výrobních postupech se forma před odléváním postříká separačním prostředkem, aby bylo zajištěno, že následně odlitý díl lze z formy snadno vyjmout. Tavenina se však nevlévá přímo do dutiny formy, ale nejprve se naplní do licí komory stroje na tlakové lití. Odtud je slitina vtlačována do formy pístem (tzv. licí soupravou) jedním nebo více kanály. Rozdíl mezi oběma procesy spočívá ve struktuře licí komory, jak je popsáno níže.
Metoda tlakového lití v horké komoře
Harakteristickým rysem strojů pro tlakové lití v horké komoře je, že licí komora je neustále v kontaktu s tekutou slitinou. Tavenina prochází ventilem do licí komory, kde je pístem vysokou rychlostí vtlačována do uzavřené licí formy. Tento proces se používá pro slitiny s nízkou teplotou tání, jako je zinek, olovo nebo cín.
Metoda tlakového lití ve studené komoře
Stroje pro tlakové lití ve studené komoře jsou konstruovány tak, že licí souprava je umístěna mimo taveninu. Při výrobě součásti se slitina naplní do licí komory a přes kanálky se vtlačí do formy pro tlakové lití. Tento postup je vhodný pro materiály s vyšší teplotou tání. Mezi ně patří například hliník a měď.
Po vtlačení slitiny do formy v obou procesech součástka pod silným tlakem ztuhne, načež lze otevřít západky formy. Díl s hradítky je z formy vyjmut automaticky ovládanými vyhazovacími kolíky a v případě potřeby může být dále zpracován. Zjednodušeně lze proces odlévání rozdělit do následujících kroků a v praxi probíhá v setinách sekundy – nebo dokonce jen v tisícinách sekundy:
- Rychlé naplnění licí formy slitinou
- Vytvrzení součásti pod vysokým tlakem
- Otevření formy a vyjmutí součásti
:quality(80)/images.vogel.de/vogelonline/bdb/1506300/1506374/original.jpg)
Studokomorové tlakové lití je nejoblíbenějším postupem při hromadné výrobě odlitků z lehkých kovů. Přečtěte si nyní o klíčových faktorech pro realizaci konceptu lehké konstrukce se sníženými náklady.
Materiály1
Při tlakovém lití se k výrobě součástí používají neželezné kovy a výběr slitiny pro konkrétní aplikaci závisí na rozpočtu, hmotnosti a vlastnostech materiálu.
Hliník je jedním z nejdůležitějších materiálů s podílem více než 80 %, následuje zinek a hořčík. However, copper, lead and tin can also be used. The alloys have different properties. For example, aluminum (600°C) and magnesium (520°C) have a high melting point, zinc (380°C) and lead (320°C) a low melting point.
Die casting alloys offer many advantages:
- High corrosion resistance
- High strength and hardness
- High thermal conductivity
- High electrical conductivity
- Very good EMI/ RFI isolation
- Good processing properties
:quality(80)/images.vogel.de/vogelonline/bdb/1317600/1317687/original.jpg)
Low-Pressure vs. High-Pressure Die Casting
Various processes are used in foundry practice. Castings can also be produced without high pressure. In the sand casting process, for example, the alloy is poured into a mold made of sand, which must be destroyed in order to reveal the manufactured component (lost foam). Při investičním lití, které se používá k výrobě velmi malých odlitků, se formy a modely (obvykle vyrobené z vosku nebo plastu) po procesu lití rovněž zničí. Dalším příkladem je gravitační lití, při němž se používá trvalá kovová forma, ale nepoužívá se vysoký tlak pro vtlačení taveniny do formy. Spíše se odlitek vyrábí nebo forma plní gravitací.
Existují také rozdíly v procesu tlakového lití. Existují například procesy, které k výrobě dílů používají buď vysoký, nebo nízký tlak. Zatímco vysokotlaké tlakové lití představuje přibližně 50 % výroby odlitků z lehkých kovů, nízkotlaké tlakové lití tvoří pouze necelých 20 % celkové výroby.2
Nízkotlaké tlakové lití využívá především slitiny s nízkými body tání. Je možné odlévat součásti o hmotnosti od 2 do 150 kg. Výhodou je, že lze dosáhnout velmi vysokých hodnot pevnosti a složitých geometrií, jakož i lepšího využití materiálu a rozměrové přesnosti. Tento proces je méně vhodný pro velmi tenkostěnné díly, protože lze dosáhnout pouze minimální tloušťky stěny 3 mm. Je třeba také zmínit, že odlévací cykly při nízkotlakém tlakovém lití jsou pomalejší než při vysokotlakém lití.
Při vysokotlakém tlakovém lití je tavenina vtlačována do formy pod vysokým tlakem a vysokou rychlostí, čímž se odlévací cyklus zrychluje. Kromě toho lze vyrábět tenkostěnné odlitky (minimální tloušťka stěny 1 mm) s hladším povrchem. Nevýhodou tohoto výrobního procesu jsou však vysoké provozní a investiční náklady, nižší hodnoty pevnosti a omezená hmotnost odlitku, protože závisí na uzavírací síle stroje.
:quality(80)/images.vogel.de/vogelonline/bdb/1508700/1508781/original.jpg)
Oblasti použití
Tlakové lití se používá především pro velkosériovou výrobu, tj. pro odlévání mnoha součástí stejného typu. Despite the high pressure used during the manufacturing process, a high casting quality is achieved. The die casting process is particularly suitable for the production of very thin (up to 1 mm) (lightweight) components.
Most commonly, die cast components are manufactured for the automotive industry, such as wheels, blocks, cylinder heads, valve blocks and manifolds. This sector accounts for around 84 % of the castings produced by German foundries. 3 The use of aluminum parts leads to a reduction in the weight of the vehicles and thus to a reduction in fuel consumption. In addition, there are other industries in which die cast parts are used:
- Aerospace
- Domestic Appliances
- Furniture
- Power Tools
- Electronics
- Machinery
- Lighting Technology
In the future, other industries such as electromobility will be of interest to foundries. To nabízí obrovský potenciál pro odlitky z lehkých kovů.4
Historie tlakového lití 5
Tlakové lití vzniklo v polovině 19. století, kdy došlo k rozkvětu vydavatelství. Cílem bylo, aby bylo možné tisknout noviny a knihy rychle, pružně a hospodárně. Patří k nim ručně ovládané zařízení, v němž bylo možné odlévat písmena ze slitiny cínu a olova (1838), rotační tiskařský stroj (1846) a nakonec linotyp (1886). Jedním z hlavních prvků tohoto stroje byl integrovaný odlévací stroj, který vléval tekuté olovo do liniových forem vyrobených z mosazných raznic na písmena. Po odlití se matrice vrátily do zásobníku matric a odlité olověné linky byly vyhozeny. Olověné linky byly poté sestaveny do stránek, které sloužily jako tiskové desky pro archový tisk nebo jako šablony pro kulaté tiskové desky potřebné pro rotační tisk.
:quality(80)/images.vogel.de/vogelonline/bdb/1475800/1475868/original.jpg)
Prvních 30 let se tlakové lití používalo prakticky výhradně v polygrafickém průmyslu. Zlom nastal, když Herman H. Doehler založil v roce 1908 společnost Doehler die casting Company, která byla na počátku 40. let 20. století považována za největšího světového výrobce tlakově litých dílů a existovala až do roku 1998. První na trhu dostupný stroj na tlakové lití, který obsahoval všechny základní součásti moderního stroje na tlakové lití, vyvinuli v roce 1925 Joseph Soss a Louis H. Morin v USA.
Během konce 19. století a prvních desetiletí 20. století přicházely na trh nové výrobky a průmyslová výroba rychle rostla. Výrobci rozpoznali výhody tlakového lití, které bylo možné využít k hospodárné výrobě dílů pro psací stroje, pokladny, hodinky a elektrické přístroje. Výrobci hraček také používali tlakové lití k výrobě hraček a modelů aut, které byly co nejvěrnější originálu. V neposlední řadě se významnými odběrateli tlakově litých výrobků stal vznikající automobilový průmysl a jeho dodavatelé.
Od počátku 20. století se technologie tlakového lití vyvíjela stále rychleji. Zpočátku se k tlakovému lití používalo především olovo a cín, dva kovy s relativně nízkou teplotou tání a dobrou tažností. Kolem roku 1914 se začalo pracovat na slitinách zinku a hliníku, které nabízely vyšší pevnost. Ve 30. letech 20. století se přidaly slitiny mědi a hořčíku. Hořčík, který se specifickou hustotou 1,74 g/cm3 váží o třetinu méně než lehký kov hliník (2,75 g/cm3) a dnes se používá především v automobilovém průmyslu, zažil svůj první rozmach jako materiál pro tlakové lití v letech 1946-1978: Z tohoto materiálu byly vyrobeny motor a převodovka vozu VW Brouk. Technologie tlakového lití však na této vývojové úrovni nezůstala. Stroje byly vybaveny zdokonalenou řídicí technikou a byly stále výkonnější. Na trh přišly nástrojové oceli se zlepšenými vlastnostmi pro výrobu forem a fyzikální vlastnosti slitin pro tlakové lití byly optimalizovány, takže dnes lze vyrábět odlitky s velmi tenkými tloušťkami stěn i vysokými mechanickými vlastnostmi. Mezi aktuální témata patří automatizace, energetická a surovinová účinnost, složité tvary, hybridní díly, automatizace procesů a digitalizace (Průmysl 4.0).
:quality(80)/images.vogel.de/vogelonline/bdb/1518000/1518051/original.jpg)
1) Dynacast, tlakové lití kovů, k dispozici na https://www.dynacast.de/druckgussmetalle-al-mg-zn
2) The Metal Casting, k dispozici na http://www.themetalcasting.com/pressure-die-casting.html
3) BD Guss, 2016
4) NürnbergMesse, 2018, k dispozici na https://www.euroguss.de/de/news/presseinformationen/zukunft-von-druckguss-7sxvrxjjb7_pireport
5) NürnbergMesse, 2018, available on https://www.euroguss.de/de/news/fachartikel/fachartikel-druckgiessen-nl2jm1fcex_pireport
Further References
KUG BD Guss, 2009, Die Casting – Series production for highly complex thin-walled light metal castings, available on https://www.kug.bdguss.de/giessverfahren-inhalte/druckguss/
Powerguss – Haus der Gießerei-Industrie, Die casting – how does it work?, available on https://www.powerguss.de/was-ist-giessen/druckguss/
Lechuga, G., 2016, Die Casting Facts Infographic, available on https://www.slideshare.net/GermnLechuga/die-casting-facts-infographic
Dynacast, die casting, available on https://www.dynacast.de/druckguss