Connaissances de base
Qu’est-ce que le moulage sous pression et comment a-t-il progressé depuis le 19e siècle ? Cette question et bien d’autres notions de base, comme l’utilisation de différents procédés et matériaux, sont expliquées dans l’article suivant.
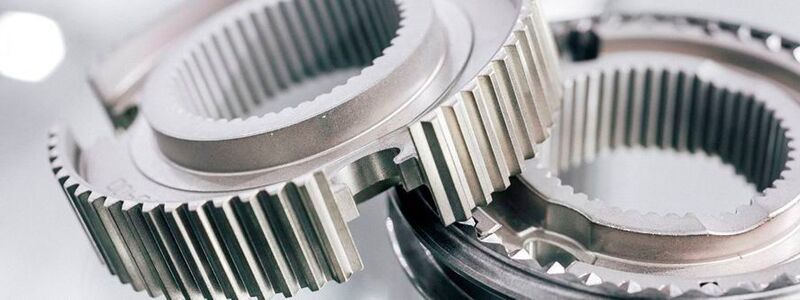
La coulée sous pression est l’un des procédés de formage les plus économiques et les plus rapides. Les avantages de ce procédé de production sont que des centaines de milliers de pièces moulées peuvent être produites relativement rapidement en utilisant un seul moule. Tous les composants produits ont une qualité uniforme et impliquent des coûts unitaires relativement faibles. Mais comment se présente exactement le processus de fabrication ? Quels matériaux peuvent être utilisés et dans quels domaines les pièces moulées sont-elles utilisées ?
Définition du « moulage sous pression »
Le moulage sous pression est un procédé de moulage automatisé dans lequel le liquide en fusion est pressé dans un moule sous haute pression (150 à 1200 bars) et à une vitesse de remplissage élevée (jusqu’à 540 km/h). On utilise généralement des alliages à faible point de fusion. Ce procédé de coulée est particulièrement adapté à la production en série et en masse de composants car, contrairement à la coulée en sable, par exemple, on utilise des moules métalliques permanents qui ne doivent pas être détruits après la coulée. Il est possible de produire des composants de grande taille et complexes avec de faibles épaisseurs de paroi.
#expert
:quality(80)/images.vogel.de/vogelonline/bdb/1420000/1420060/original.jpg)
Moules
Les moules de coulée sous pression, fabriqués à partir de nuances d’acier de haute qualité et résistant à la chaleur, se composent de deux moitiés qui forment une cavité dans laquelle le liquide en fusion est pressé pendant le processus de coulée. Les moitiés sont situées sur une plaque de machine fixe et une plaque mobile. Pendant le processus de coulée, une pression élevée est appliquée aux moitiés du moule, c’est pourquoi le moule est équipé de verrous. En outre, certaines parties du moule sont refroidies et/ou chauffées afin que la coulée se solidifie comme souhaité. La production des moules est très coûteuse et prend beaucoup de temps, mais plusieurs dizaines de milliers à plus d’un million de pièces peuvent être produites avec un seul d’entre eux. Un autre avantage des moules de coulée réutilisables est que la fonte se refroidit rapidement.
Fonctionnalité et procédures
Dans la coulée sous pression, il existe deux façons différentes de fabriquer des composants : la coulée sous pression en chambre chaude et la coulée sous pression en chambre froide. Dans les deux procédés de fabrication, le moule est pulvérisé d’un agent de démoulage avant le processus de coulée afin de garantir que la pièce coulée par la suite puisse être facilement démoulée. Toutefois, la masse fondue n’est pas versée directement dans la cavité du moule, mais est d’abord remplie dans la chambre de coulée de la machine à couler sous pression. De là, l’alliage est pressé dans le moule par un piston (appelé ensemble de coulée) à travers un ou plusieurs canaux. La différence entre les deux procédés réside dans la structure de la chambre de coulée, comme décrit ci-dessous.
Méthode de coulée sous pression à chambre chaude
La caractéristique des machines de coulée sous pression à chambre chaude est que la chambre de coulée est constamment en contact avec l’alliage liquide. La masse fondue passe par une vanne dans la chambre de coulée, où elle est pressée à grande vitesse dans le moule de coulée sous pression fermé par le piston. Ce procédé est utilisé pour les alliages à faible point de fusion, comme le zinc, le plomb ou l’étain.
Méthode de moulage sous pression à chambre froide
Les machines de moulage sous pression à chambre froide sont conçues de telle sorte que l’ensemble de moulage est situé à l’extérieur de la masse fondue. Pour produire un composant, l’alliage est rempli dans la chambre de coulée et pressé dans le moule de coulée sous pression à travers des canaux. Ce procédé est adapté aux matériaux dont le point de fusion est élevé. Il s’agit, par exemple, de l’aluminium et du cuivre.
Après que l’alliage a été pressé dans le moule dans les deux procédés, le composant se solidifie sous la forte pression, après quoi les verrous du moule peuvent être ouverts. La pièce avec porte est retirée du moule par des broches d’éjection actionnées automatiquement et peut être traitée ultérieurement si nécessaire. En termes simples, le processus de moulage peut être divisé en étapes suivantes et se déroule en pratique en centièmes de seconde – voire seulement en millièmes de seconde :
- Remplissage rapide du moule de coulée avec l’alliage
- Durcissement du composant sous haute pression
- Ouverture du moule et retrait du composant
:quality(80)/images.vogel.de/vogelonline/bdb/1506300/1506374/original.jpg)
Le moulage sous pression en chambre froide est le procédé le plus populaire pour la production en série de pièces en métal léger. Lisez maintenant les facteurs clés pour la réalisation d’un concept de conception légère à coût réduit.
Matériaux1
Dans le moulage sous pression, les métaux non ferreux sont utilisés pour fabriquer des composants, et le choix de l’alliage pour une application particulière dépend du budget, du poids et des propriétés du matériau.
L’aluminium est l’un des matériaux les plus importants avec une part de plus de 80 %, suivi du zinc et du magnésium. However, copper, lead and tin can also be used. The alloys have different properties. For example, aluminum (600°C) and magnesium (520°C) have a high melting point, zinc (380°C) and lead (320°C) a low melting point.
Die casting alloys offer many advantages:
- High corrosion resistance
- High strength and hardness
- High thermal conductivity
- High electrical conductivity
- Very good EMI/ RFI isolation
- Good processing properties
:quality(80)/images.vogel.de/vogelonline/bdb/1317600/1317687/original.jpg)
Low-Pressure vs. High-Pressure Die Casting
Various processes are used in foundry practice. Castings can also be produced without high pressure. In the sand casting process, for example, the alloy is poured into a mold made of sand, which must be destroyed in order to reveal the manufactured component (lost foam). Dans le moulage à la cire perdue, qui est utilisé pour fabriquer de très petites pièces moulées, les moules et les modèles (généralement en cire ou en plastique) sont également détruits après le processus de moulage. Un autre exemple est la coulée sous pression par gravité, qui utilise un moule métallique permanent mais n’utilise pas de haute pression pour presser la masse fondue dans le moule. Au contraire, le moulage est fabriqué ou le moule rempli par gravité.
Il existe également des différences dans le processus de moulage sous pression. Par exemple, il existe des procédés qui utilisent soit une haute ou une basse pression pour produire les composants. Alors que le moulage sous haute pression représente environ 50 % de la production de pièces en métal léger, le moulage sous basse pression ne représente qu’un peu moins de 20 % de la production totale.2
Le moulage sous basse pression utilise principalement des alliages à faible point de fusion. Il est possible de couler des composants de 2 à 150 kg. Les avantages sont que l’on peut obtenir des valeurs de résistance très élevées et des géométries complexes, ainsi qu’une meilleure utilisation des matériaux et une meilleure précision dimensionnelle. Ce procédé est moins adapté aux pièces à parois très fines, car il ne permet d’obtenir qu’une épaisseur de paroi minimale de 3 mm. Il convient également de mentionner que les cycles de coulée utilisant le moulage sous basse pression sont plus lents que ceux sous haute pression.
Dans le moulage sous haute pression, la matière fondue est pressée dans le moule sous haute pression et à grande vitesse, ce qui accélère le cycle de coulée. En outre, il est possible de produire des pièces moulées à paroi plus mince (épaisseur minimale de 1 mm) avec des surfaces plus lisses. L’inconvénient de ce procédé de fabrication réside toutefois dans les coûts d’exploitation et d’investissement élevés, les valeurs de résistance sont plus faibles et le poids de la pièce moulée sous pression est limité car il dépend de la force de fermeture de la machine.
:quality(80)/images.vogel.de/vogelonline/bdb/1508700/1508781/original.jpg)
Domaines d’application
La coulée sous pression est principalement utilisée pour la production en grande série, c’est-à-dire pour de nombreux composants du même type à couler. Despite the high pressure used during the manufacturing process, a high casting quality is achieved. The die casting process is particularly suitable for the production of very thin (up to 1 mm) (lightweight) components.
Most commonly, die cast components are manufactured for the automotive industry, such as wheels, blocks, cylinder heads, valve blocks and manifolds. This sector accounts for around 84 % of the castings produced by German foundries. 3 The use of aluminum parts leads to a reduction in the weight of the vehicles and thus to a reduction in fuel consumption. In addition, there are other industries in which die cast parts are used:
- Aerospace
- Domestic Appliances
- Furniture
- Power Tools
- Electronics
- Machinery
- Lighting Technology
In the future, other industries such as electromobility will be of interest to foundries. Cela offre un énorme potentiel pour les moulages de métaux légers.4
Histoire des moulages sous pression 5
Les moulages sous pression sont nés au milieu du 19ème siècle, lorsque l’édition était florissante. L’objectif était de pouvoir imprimer des journaux et des livres de manière rapide, souple et rentable. On peut citer un dispositif manuel permettant de couler un alliage d’étain et de plomb dans les lettres (1838), la presse à imprimer rotative (1846) et enfin la machine à composer Linotype (1886). L’un des principaux éléments de cette machine était une machine de coulée sous pression intégrée qui versait du plomb liquide dans les moules de ligne constitués de matrices de lettres en laiton. Après la coulée, les matrices étaient renvoyées dans le magasin de matrices et les lignes de plomb coulées étaient éjectées. Les lignes de plomb étaient ensuite assemblées en pages qui servaient de plaques d’impression pour l’impression sur feuilles ou de gabarits pour les plaques d’impression rondes nécessaires au processus d’impression rotative.
:quality(80)/images.vogel.de/vogelonline/bdb/1475800/1475868/original.jpg)
Pendant les 30 premières années, le moulage sous pression était pratiquement exclusivement utilisé dans l’industrie de l’impression. Le tournant s’est produit lorsque Herman H. Doehler a fondé la Doehler die casting Company en 1908, qui, au début des années 1940, était considérée comme le plus grand fabricant de pièces moulées sous pression au monde et a existé jusqu’en 1998. La première machine de moulage sous pression disponible sur le marché, qui contenait tous les composants essentiels d’une machine de moulage sous pression moderne, a été développée en 1925 par Joseph Soss et Louis H. Morin aux États-Unis.
Pendant la fin du 19e siècle et les premières décennies du 20e siècle, de nouveaux produits sont arrivés sur le marché et la production industrielle a connu une croissance rapide. Les fabricants ont reconnu les avantages du moulage sous pression, qui pouvait être utilisé pour produire économiquement des pièces pour les machines à écrire, les caisses enregistreuses, les montres et les appareils électriques. Les fabricants de jouets ont également utilisé le moulage sous pression pour produire des jouets et des modèles réduits de voitures aussi fidèles que possible à l’original. Enfin, l’industrie automobile émergente et ses fournisseurs sont devenus d’importants acheteurs de produits moulés sous pression.
Depuis le début du 20e siècle, la technologie du moulage sous pression a progressé à une vitesse croissante. Au départ, le plomb et l’étain, deux métaux ayant une température de fusion relativement basse et une bonne ductilité, étaient principalement utilisés dans le moulage sous pression. Vers 1914, on a commencé à travailler sur les alliages de zinc et d’aluminium, qui offraient une plus grande résistance. Les alliages de cuivre et de magnésium ont été ajoutés dans les années 1930. Le magnésium, qui, avec une densité spécifique de 1,74 g/cm3, pèse un tiers de moins que le métal léger qu’est l’aluminium (2,75 g/cm3) et qui est aujourd’hui utilisé principalement dans l’industrie automobile, a connu son premier essor en tant que matériau de moulage sous pression entre 1946 et 1978 : Le moteur et la boîte de vitesses de la Coccinelle VW étaient fabriqués dans ce matériau. Cependant, la technologie du moulage sous pression ne s’est pas arrêtée à ce niveau de développement. Les machines ont été équipées d’une technologie de commande raffinée et sont devenues de plus en plus puissantes. Des aciers à outils aux propriétés améliorées sont apparus sur le marché pour la fabrication des moules, et les propriétés physiques des alliages de coulée sous pression ont été optimisées, de sorte qu’il est aujourd’hui possible de produire des pièces moulées présentant à la fois des épaisseurs de paroi très fines et des propriétés mécaniques élevées. Parmi les sujets d’actualité figurent l’automatisation, l’efficacité énergétique et des matières premières, les formes complexes, les pièces hybrides, l’automatisation des processus et la numérisation (industrie 4.0).
:quality(80)/images.vogel.de/vogelonline/bdb/1518000/1518051/original.jpg)
1) Dynacast, métaux moulés sous pression, disponible sur https://www.dynacast.de/druckgussmetalle-al-mg-zn
2) La fonderie de métaux, disponible sur http://www.themetalcasting.com/pressure-die-casting.html
3) BD Guss, 2016
4) NürnbergMesse, 2018, disponible sur https://www.euroguss.de/de/news/presseinformationen/zukunft-von-druckguss-7sxvrxjjb7_pireport
5) NürnbergMesse, 2018, available on https://www.euroguss.de/de/news/fachartikel/fachartikel-druckgiessen-nl2jm1fcex_pireport
Further References
KUG BD Guss, 2009, Die Casting – Series production for highly complex thin-walled light metal castings, available on https://www.kug.bdguss.de/giessverfahren-inhalte/druckguss/
Powerguss – Haus der Gießerei-Industrie, Die casting – how does it work?, available on https://www.powerguss.de/was-ist-giessen/druckguss/
Lechuga, G., 2016, Die Casting Facts Infographic, available on https://www.slideshare.net/GermnLechuga/die-casting-facts-infographic
Dynacast, die casting, available on https://www.dynacast.de/druckguss