Conoscenze di base
Che cos’è la pressofusione e come si è evoluta dal XIX secolo? Questo e molte altre nozioni di base come l’uso di diversi processi e materiali sono spiegati nel seguente articolo.
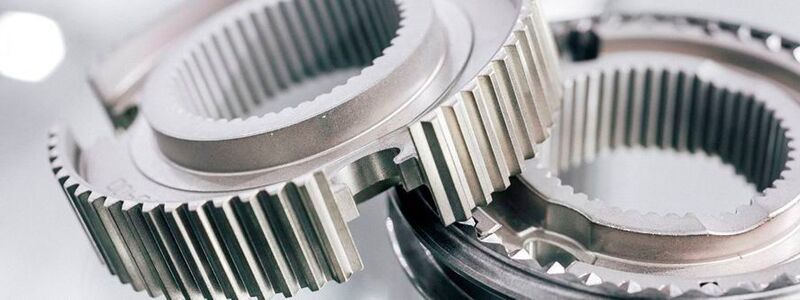
La pressofusione è uno dei processi di formatura più economici e più rapidi. I vantaggi di questo processo di produzione sono che centinaia di migliaia di getti possono essere prodotti in tempi relativamente brevi utilizzando un solo stampo. Tutti i componenti prodotti hanno una qualità uniforme e comportano costi unitari relativamente bassi. Ma come si presenta esattamente il processo di produzione? Quali materiali possono essere usati e in quali settori vengono utilizzati i getti?
Definizione di “Pressofusione”
La pressofusione è un processo di fusione automatizzato in cui il liquido fuso viene pressato in uno stampo sotto alta pressione (da 150 a 1200 bar) e ad un’alta velocità di riempimento (fino a 540 km/h). Di solito si usano leghe con un basso punto di fusione. Questo processo di colata è particolarmente adatto per la produzione in serie e di massa di componenti perché, a differenza della colata in sabbia, per esempio, vengono utilizzati stampi metallici permanenti che non devono essere distrutti dopo la colata. È possibile produrre componenti grandi e complessi con bassi spessori di parete.
#expert
:quality(80)/images.vogel.de/vogelonline/bdb/1420000/1420060/original.jpg)
Stampi
Gli stampi per la pressofusione, realizzati in acciaio di alta qualità e resistenti al calore, sono costituiti da due metà che formano una cavità in cui il liquido fuso viene premuto durante il processo di fusione. Le metà sono situate su una piastra fissa e una mobile della macchina. Durante il processo di colata, una pressione elevata viene applicata alle metà dello stampo, motivo per cui lo stampo è dotato di chiusure. Inoltre, alcune parti dello stampo vengono raffreddate e/o riscaldate in modo che la colata si solidifichi come desiderato. La produzione degli stampi è molto costosa e richiede tempo, ma con uno solo di essi si possono produrre da diverse decine di migliaia a più di un milione di pezzi fusi. Un ulteriore vantaggio degli stampi di colata riutilizzabili è che la colata si raffredda rapidamente.
Funzionalità e procedure
Nella pressofusione, ci sono due modi diversi di produrre componenti: la pressofusione a camera calda e a camera fredda. In entrambi i processi di produzione, lo stampo viene spruzzato con un agente di rilascio prima del processo di colata per assicurare che la parte successivamente colata possa essere facilmente rimossa dallo stampo. Tuttavia, la massa fusa non viene versata direttamente nella cavità dello stampo, ma viene prima riempita nella camera di colata della macchina di pressofusione. Da lì, la lega viene premuta nello stampo da un pistone (il cosiddetto set di colata) attraverso uno o più canali. La differenza tra i due processi sta nella struttura della camera di colata, come descritto di seguito.
Metodo di pressofusione a camera calda
Una caratteristica delle macchine di pressofusione a camera calda è che la camera di colata è costantemente in contatto con la lega liquida. La massa fusa passa attraverso una valvola nella camera di colata, dove viene premuta ad alta velocità nello stampo chiuso di pressofusione dal pistone. Questo processo è usato per leghe con un basso punto di fusione, come lo zinco, il piombo o lo stagno.
Metodo di pressofusione a camera fredda
Le macchine di pressofusione a camera fredda sono progettate in modo tale che il set di fusione si trova al di fuori della massa fusa. Per produrre un componente, la lega viene riempita nella camera di colata e pressata nello stampo di pressofusione attraverso dei canali. Questo processo è adatto a materiali con un punto di fusione più alto. Questi includono, per esempio, alluminio e rame.
Dopo che la lega è stata pressata nello stampo in entrambi i processi, il componente si solidifica sotto la forte pressione, dopodiché i fermi dello stampo possono essere aperti. Il pezzo con il cancello viene rimosso dallo stampo mediante perni di espulsione azionati automaticamente e può essere ulteriormente lavorato se necessario. In parole semplici, il processo di colata può essere diviso nei seguenti passi e in pratica si svolge in centesimi di secondo – o anche solo millesimi di secondo:
- Riempimento rapido dello stampo di colata con la lega
- Induritura del componente sotto alta pressione
- Apertura dello stampo e rimozione del componente
:quality(80)/images.vogel.de/vogelonline/bdb/1506300/1506374/original.jpg)
La pressofusione a camera fredda è il processo più popolare nella produzione di massa di getti di metallo leggero. Leggete ora i fattori chiave per la realizzazione di un concetto di design leggero a costi ridotti.
Materiali1
Nella pressofusione, si usano metalli non ferrosi per produrre componenti, e la scelta della lega per una particolare applicazione dipende dal budget, dal peso e dalle proprietà del materiale.
L’alluminio è uno dei materiali più importanti con una quota di oltre l’80%, seguito da zinco e magnesio. However, copper, lead and tin can also be used. The alloys have different properties. For example, aluminum (600°C) and magnesium (520°C) have a high melting point, zinc (380°C) and lead (320°C) a low melting point.
Die casting alloys offer many advantages:
- High corrosion resistance
- High strength and hardness
- High thermal conductivity
- High electrical conductivity
- Very good EMI/ RFI isolation
- Good processing properties
:quality(80)/images.vogel.de/vogelonline/bdb/1317600/1317687/original.jpg)
Low-Pressure vs. High-Pressure Die Casting
Various processes are used in foundry practice. Castings can also be produced without high pressure. In the sand casting process, for example, the alloy is poured into a mold made of sand, which must be destroyed in order to reveal the manufactured component (lost foam). Nella fusione a cera persa, che è usata per produrre parti fuse molto piccole, gli stampi e i modelli (di solito fatti di cera o plastica) sono anch’essi distrutti dopo il processo di fusione. Un altro esempio è il Gravity Die Casting, che usa uno stampo di metallo permanente ma non usa l’alta pressione per premere la colata nello stampo. Piuttosto, la colata viene prodotta o lo stampo riempito per gravità.
Ci sono anche differenze nel processo di pressofusione. Per esempio, ci sono processi che usano alta o bassa pressione per produrre i componenti. Mentre la pressofusione ad alta pressione rappresenta circa il 50% della produzione di metallo leggero, la pressofusione a bassa pressione rappresenta solo poco meno del 20% della produzione totale.2
La pressofusione a bassa pressione utilizza principalmente leghe con bassi punti di fusione. È possibile fondere componenti da 2 a 150 kg. I vantaggi sono che si possono ottenere valori di resistenza molto alti e geometrie complesse, così come un migliore utilizzo del materiale e la precisione dimensionale. Il processo è meno adatto per pezzi con pareti molto sottili, poiché si può ottenere solo uno spessore minimo di 3 mm. Va anche detto che i cicli di colata con la pressofusione a bassa pressione sono più lenti di quelli ad alta pressione.
Nella pressofusione ad alta pressione, la massa fusa viene pressata nello stampo ad alta pressione e ad alta velocità, accelerando così il ciclo di colata. Inoltre, si possono produrre getti con pareti più sottili (spessore minimo di 1 mm) e superfici più lisce. Lo svantaggio di questo processo di produzione, tuttavia, è che si devono sostenere elevati costi operativi e di investimento, i valori di resistenza sono inferiori e il peso della pressofusione è limitato perché dipende dalla forza di chiusura della macchina.
:quality(80)/images.vogel.de/vogelonline/bdb/1508700/1508781/original.jpg)
Campi di applicazione
La pressofusione è utilizzata principalmente per la produzione di grandi serie, cioè per molti componenti dello stesso tipo da fondere. Despite the high pressure used during the manufacturing process, a high casting quality is achieved. The die casting process is particularly suitable for the production of very thin (up to 1 mm) (lightweight) components.
Most commonly, die cast components are manufactured for the automotive industry, such as wheels, blocks, cylinder heads, valve blocks and manifolds. This sector accounts for around 84 % of the castings produced by German foundries. 3 The use of aluminum parts leads to a reduction in the weight of the vehicles and thus to a reduction in fuel consumption. In addition, there are other industries in which die cast parts are used:
- Aerospace
- Domestic Appliances
- Furniture
- Power Tools
- Electronics
- Machinery
- Lighting Technology
In the future, other industries such as electromobility will be of interest to foundries. Questo offre un enorme potenziale per le fusioni di metalli leggeri.4
Storia della pressofusione 5
La pressofusione è nata a metà del XIX secolo, quando l’editoria era fiorente. Lo scopo era quello di poter stampare giornali e libri in modo rapido, flessibile ed economico. Tra questi, un dispositivo azionato manualmente in cui una lega di stagno e piombo poteva essere fusa in lettere (1838), la macchina da stampa rotativa (1846) e infine la macchina per la composizione tipografica Linotype (1886). Uno degli elementi principali di questa macchina era una macchina integrata per la pressofusione che versava piombo liquido nelle matrici di lettere in ottone. Dopo la fusione, le matrici venivano riportate nel magazzino delle matrici e le linee di piombo fuse venivano espulse. Le linee di piombo venivano poi assemblate in pagine che servivano come piastre di stampa per la stampa a foglio o come modelli per le piastre di stampa rotonde necessarie per il processo di stampa rotativa.
:quality(80)/images.vogel.de/vogelonline/bdb/1475800/1475868/original.jpg)
Durante i primi 30 anni, la pressofusione fu usata praticamente solo nell’industria della stampa. La svolta avvenne quando Herman H. Doehler fondò nel 1908 la Doehler die casting Company, che all’inizio degli anni ’40 era considerata il più grande produttore mondiale di pezzi pressofusi ed è esistita fino al 1998. La prima macchina di pressofusione disponibile sul mercato, che conteneva tutti i componenti essenziali di una moderna macchina di pressofusione, fu sviluppata nel 1925 da Joseph Soss e Louis H. Morin negli Stati Uniti.
Durante la fine del XIX secolo e i primi decenni del XX secolo, nuovi prodotti arrivarono sul mercato e la produzione industriale crebbe rapidamente. I produttori riconobbero i vantaggi della pressofusione, che poteva essere usata per produrre economicamente parti per macchine da scrivere, registratori di cassa, orologi e apparecchi elettrici. Anche i produttori di giocattoli usarono la pressofusione per produrre automobili giocattolo e modellini che fossero il più possibile fedeli all’originale. Infine, ma non meno importante, l’industria automobilistica emergente e i suoi fornitori divennero importanti acquirenti di prodotti pressofusi.
Dall’inizio del XX secolo, la tecnologia della pressofusione è progredita con sempre maggiore velocità. Inizialmente, il piombo e lo stagno, due metalli con una temperatura di fusione relativamente bassa e una buona duttilità, erano principalmente usati nella pressofusione. Intorno al 1914, si iniziò a lavorare su leghe di zinco e alluminio, che offrivano una maggiore resistenza. Le leghe di rame e magnesio furono aggiunte negli anni ’30. Il magnesio, che con una densità specifica di 1,74 g/cm3 pesa un terzo in meno del metallo leggero alluminio (2,75 g/cm3) ed è usato oggi soprattutto nell’industria automobilistica, ha vissuto il suo primo boom come materiale di pressofusione tra il 1946 e il 1978: Il motore e il cambio del Maggiolino VW erano fatti di questo materiale. Tuttavia, la tecnologia della pressofusione non ha indugiato su questo livello di sviluppo. Le macchine furono dotate di una tecnologia di controllo raffinata e divennero sempre più potenti. Acciai per utensili con proprietà migliorate entrarono sul mercato per la produzione di stampi, e le proprietà fisiche delle leghe per la pressofusione furono ottimizzate in modo che oggi si possono produrre pezzi fusi con spessori di parete molto sottili ed elevate proprietà meccaniche. I temi attuali comprendono l’automazione, l’efficienza energetica e delle materie prime, le forme complesse, le parti ibride, l’automazione dei processi e la digitalizzazione (Industria 4.0).
:quality(80)/images.vogel.de/vogelonline/bdb/1518000/1518051/original.jpg)
1) Dynacast, metalli pressofusi, disponibile su https://www.dynacast.de/druckgussmetalle-al-mg-zn
2) La fusione dei metalli, disponibile su http://www.themetalcasting.com/pressure-die-casting.html
3) BD Guss, 2016
4) NürnbergMesse, 2018, disponibile su https://www.euroguss.de/de/news/presseinformationen/zukunft-von-druckguss-7sxvrxjjb7_pireport
5) NürnbergMesse, 2018, available on https://www.euroguss.de/de/news/fachartikel/fachartikel-druckgiessen-nl2jm1fcex_pireport
Further References
KUG BD Guss, 2009, Die Casting – Series production for highly complex thin-walled light metal castings, available on https://www.kug.bdguss.de/giessverfahren-inhalte/druckguss/
Powerguss – Haus der Gießerei-Industrie, Die casting – how does it work?, available on https://www.powerguss.de/was-ist-giessen/druckguss/
Lechuga, G., 2016, Die Casting Facts Infographic, available on https://www.slideshare.net/GermnLechuga/die-casting-facts-infographic
Dynacast, die casting, available on https://www.dynacast.de/druckguss