Grundläggande kunskaper
Vad är pressgjutning och hur har utvecklingen gått sedan 1800-talet? Detta och många andra grunder som till exempel användningen av olika processer och material förklaras i följande artikel.
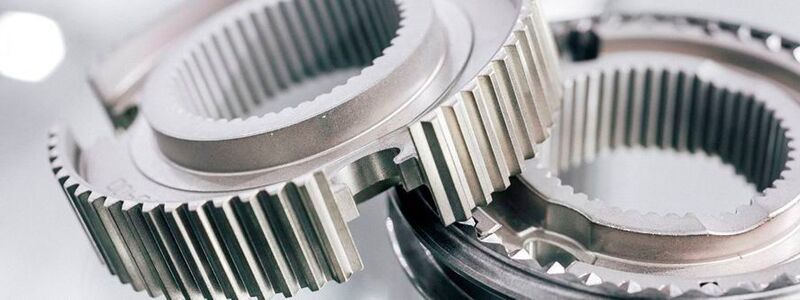
Die gjutning är en av de mest ekonomiska och snabbaste formningsprocesserna. Fördelarna med denna produktionsprocess är att hundratusentals gjutgods kan tillverkas relativt snabbt med hjälp av endast en gjutform. Alla tillverkade komponenter har en enhetlig kvalitet och medför relativt låga enhetskostnader. Men hur exakt ser tillverkningsprocessen ut? Vilka material kan användas och inom vilka områden används gjutgodset?
Definition av ”Die Casting”
Die casting är en automatiserad gjutprocess där den flytande smältan pressas in i en gjutform under högt tryck (150-1200 bar) och med hög fyllningshastighet (upp till 540 km/h). Vanligtvis används legeringar med låg smältpunkt. Denna gjutprocess är särskilt lämplig för serie- och massproduktion av komponenter eftersom man, till skillnad från t.ex. sandgjutning, använder permanenta metallformar som inte behöver förstöras efter gjutningen. Det är möjligt att tillverka stora och komplexa komponenter med låga väggtjocklekar.
#expert
:quality(80)/images.vogel.de/vogelonline/bdb/1420000/1420060/original.jpg)
Gjutformar
Den gjutformar för pressgjutning, som är tillverkade av högkvalitativa, värmebeständiga stålsorter, består av två halvor som bildar ett hålrum i vilket den flytande smältan pressas in under gjutprocessen. Halvorna är placerade på en fast och en rörlig maskinplatta. Under gjutningsprocessen appliceras ett högt tryck på formhalvorna, vilket är anledningen till att formen är utrustad med spärrar. Dessutom kyls och/eller värms vissa delar av formen så att gjutgodset stelnar på önskat sätt. Tillverkningen av formarna är mycket dyr och tidskrävande, men flera tiotusentals till över en miljon gjutgods kan tillverkas med bara en av dem. En ytterligare fördel med de återanvändbara gjutformarna är att smältan kyls ner snabbt.
Funktionalitet och förfaranden
I pressgjutning finns det två olika sätt att tillverka komponenter: pressgjutning med varmkammare och pressgjutning med kallkammare. I båda tillverkningsprocesserna sprutas formen med ett släppmedel före gjutningen för att se till att den senare gjutna delen lätt kan avlägsnas från formen. Smältan hälls dock inte direkt i formhålan utan fylls först i gjutkammaren i pressgjutningsmaskinen. Därefter pressas legeringen in i formen med hjälp av en kolv (den så kallade gjutuppsättningen) genom en eller flera kanaler. Skillnaden mellan de två processerna ligger i gjutkammarens uppbyggnad, vilket beskrivs nedan.
Hot Chamber Die Casting Method
Ett karakteristiskt kännetecken för pressgjutmaskiner med varm kammare är att gjutkammaren ständigt är i kontakt med den flytande legeringen. Smältan passerar genom en ventil in i gjutkammaren, där den med hög hastighet pressas in i den slutna gjutformen av kolven. Denna process används för legeringar med låg smältpunkt, t.ex. zink, bly eller tenn.
Kallkammarformgjutningsmetod
Kallkammarformgjutningsmaskiner är konstruerade på ett sådant sätt att gjutuppsättningen är placerad utanför smältan. För att tillverka en komponent fylls legeringen i gjutkammaren och pressas in i gjutformen genom kanaler. Denna process är lämplig för material med en högre smältpunkt. Dessa inkluderar till exempel aluminium och koppar.
När legeringen har pressats in i formen i båda processerna stelnar komponenten under det starka trycket, varpå formens spärrar kan öppnas. Delen med grind avlägsnas ur formen med hjälp av automatiskt manövrerade utkaststift och kan vid behov bearbetas ytterligare. Med enkla ord kan gjutprocessen delas in i följande steg och sker i praktiken på hundradelar av en sekund – eller till och med bara tusendelar av en sekund:
- Snabb fyllning av gjutformen med legeringen
- Härdning av komponenten under högt tryck
- Öppning av formen och avlägsnande av komponenten
:quality(80)/images.vogel.de/vogelonline/bdb/1506300/1506374/original.jpg)
Kallkammarformgjutning är den mest populära processen för massproduktion av gjutgods av lättmetall. Läs nu om de viktigaste faktorerna för att förverkliga ett kostnadsreducerat lättviktskoncept.
Material1
I pressgjutning används icke-järnmetaller för att tillverka komponenter, och valet av legering för en viss tillämpning beror på budget, vikt och materialegenskaper.
Aluminium är ett av de viktigaste materialen med en andel på mer än 80 %, följt av zink och magnesium. However, copper, lead and tin can also be used. The alloys have different properties. For example, aluminum (600°C) and magnesium (520°C) have a high melting point, zinc (380°C) and lead (320°C) a low melting point.
Die casting alloys offer many advantages:
- High corrosion resistance
- High strength and hardness
- High thermal conductivity
- High electrical conductivity
- Very good EMI/ RFI isolation
- Good processing properties
:quality(80)/images.vogel.de/vogelonline/bdb/1317600/1317687/original.jpg)
Low-Pressure vs. High-Pressure Die Casting
Various processes are used in foundry practice. Castings can also be produced without high pressure. In the sand casting process, for example, the alloy is poured into a mold made of sand, which must be destroyed in order to reveal the manufactured component (lost foam). Vid investeringsgjutning, som används för att tillverka mycket små gjutna delar, förstörs också formarna och modellerna (vanligen gjorda av vax eller plast) efter gjutningen. Ett annat exempel är Gravity Die Casting, där man använder en permanent metallform men inte använder högt tryck för att pressa in smältan i formen. I stället tillverkas gjutgodset eller fylls formen med hjälp av gravitationen.
Det finns också skillnader i formgjutningsprocessen. Det finns till exempel processer som använder antingen högt eller lågt tryck för att tillverka komponenterna. Medan högtrycksformgjutning står för cirka 50 % av produktionen av lättmetallgjutning står lågtrycksformgjutning endast för knappt 20 % av den totala produktionen.2
Lågtrycksformgjutning använder främst legeringar med låg smältpunkt. Det är möjligt att gjuta komponenter från 2 till 150 kg. Fördelarna är att mycket höga hållfasthetsvärden och komplexa geometrier samt förbättrat materialutnyttjande och måttnoggrannhet kan uppnås. Processen är mindre lämplig för mycket tunnväggiga delar, eftersom endast en minsta väggtjocklek på 3 mm kan uppnås. Det bör också nämnas att gjutcyklerna med lågtrycksformgjutning är långsammare än de med högt tryck.
Vid högtrycksformgjutning pressas smältan in i formen under högt tryck och med hög hastighet, vilket påskyndar gjutcykeln. Dessutom kan tunnare gjutgods (minsta väggtjocklek 1 mm) med slätare ytor tillverkas. Nackdelen med denna tillverkningsprocess är dock att den medför höga drifts- och investeringskostnader, att hållfasthetsvärdena är lägre och att pressgjutningens vikt är begränsad eftersom den beror på maskinens stängningskraft.
:quality(80)/images.vogel.de/vogelonline/bdb/1508700/1508781/original.jpg)
Användningsområden
Die gjutning av pressgjutgods används främst för stor serietillverkning, dvs. för många komponenter av samma typ som ska gjutas. Despite the high pressure used during the manufacturing process, a high casting quality is achieved. The die casting process is particularly suitable for the production of very thin (up to 1 mm) (lightweight) components.
Most commonly, die cast components are manufactured for the automotive industry, such as wheels, blocks, cylinder heads, valve blocks and manifolds. This sector accounts for around 84 % of the castings produced by German foundries. 3 The use of aluminum parts leads to a reduction in the weight of the vehicles and thus to a reduction in fuel consumption. In addition, there are other industries in which die cast parts are used:
- Aerospace
- Domestic Appliances
- Furniture
- Power Tools
- Electronics
- Machinery
- Lighting Technology
In the future, other industries such as electromobility will be of interest to foundries. Detta erbjuder en enorm potential för gjutgods av lättmetall.4
Dryckgjutningens historia 5
Dryckgjutning uppstod i mitten av 1800-talet, när förlagsverksamheten blomstrade. Målet var att kunna trycka tidningar och böcker snabbt, flexibelt och kostnadseffektivt. Det handlar bland annat om en manuellt manövrerad anordning där en legering av tenn och bly kunde gjutas till bokstäver (1838), den roterande tryckpressen (1846) och slutligen Linotype-sättmaskinen (1886). En av de viktigaste delarna i denna maskin var en integrerad formgjutningsmaskin som hällde flytande bly i linjeformar gjorda av bokstavsformar i mässing. Efter gjutningen återfördes matriserna till matrismagasinet och de gjutna blylinjerna kastades ut. Blylinjerna sattes sedan ihop till sidor som fungerade som tryckplattor för arkutskrift eller som mallar för de runda tryckplattor som krävdes för rotationstryckprocessen.
:quality(80)/images.vogel.de/vogelonline/bdb/1475800/1475868/original.jpg)
Under de första 30 åren användes pressgjutning praktiskt taget uteslutande inom tryckeribranschen. Vändpunkten kom när Herman H. Doehler 1908 grundade Doehler die casting Company, som i början av 1940-talet betraktades som världens största tillverkare av pressgjutna delar och som existerade fram till 1998. Den första pressgjutningsmaskinen som fanns på marknaden och som innehöll alla väsentliga komponenter i en modern pressgjutningsmaskin utvecklades 1925 av Joseph Soss och Louis H. Morin i USA.
Under slutet av 1800-talet och 1900-talets första decennier kom nya produkter ut på marknaden och den industriella produktionen växte snabbt. Tillverkare insåg fördelarna med pressgjutning, som kunde användas för att ekonomiskt producera delar till skrivmaskiner, kassaregister, klockor och elektriska apparater. Leksakstillverkare använde sig också av pressgjutning för att tillverka leksaksbilar och modellbilar som var så lika originalet som möjligt. Sist men inte minst blev den framväxande bilindustrin och dess underleverantörer viktiga köpare av pressgjutna produkter.
Sedan början av 1900-talet har pressgjutningstekniken utvecklats allt snabbare. Till en början användes främst bly och tenn, två metaller med relativt låg smälttemperatur och god duktilitet, vid pressgjutning. Omkring 1914 började man arbeta med zink- och aluminiumlegeringar, som erbjöd högre hållfasthet. Koppar- och magnesiumlegeringar tillkom på 1930-talet. Magnesium, som med en specifik densitet på 1,74 g/cm3 väger en tredjedel mindre än lättmetallen aluminium (2,75 g/cm3) och som i dag främst används inom bilindustrin, upplevde sin första boom som pressgjutningsmaterial mellan 1946 och 1978: Det är ett material som användes i gjutformsindustrin mellan 1978 och 1978. Djupgjutningstekniken stannade dock inte kvar på denna utvecklingsnivå. Maskinerna utrustades med förfinad styrteknik och blev allt mer kraftfulla. Verktygsstål med förbättrade egenskaper kom ut på marknaden för formtillverkning, och de fysikaliska egenskaperna hos pressgjutningslegeringar optimerades så att man idag kan tillverka gjutna delar med både mycket tunna väggtjocklekar och höga mekaniska egenskaper. Aktuella ämnen är automatisering, energi- och råvarueffektivitet, komplexa former, hybriddelar, processautomatisering och digitalisering (industri 4.0).
:quality(80)/images.vogel.de/vogelonline/bdb/1518000/1518051/original.jpg)
1) Dynacast, pressgjutna metaller, finns på https://www.dynacast.de/druckgussmetalle-al-mg-zn
2) The Metal Casting, tillgänglig på http://www.themetalcasting.com/pressure-die-casting.html
3) BD Guss, 2016
4) NürnbergMesse, 2018, tillgänglig på https://www.euroguss.de/de/news/presseinformationen/zukunft-von-druckguss-7sxvrxjjb7_pireport
5) NürnbergMesse, 2018, available on https://www.euroguss.de/de/news/fachartikel/fachartikel-druckgiessen-nl2jm1fcex_pireport
Further References
KUG BD Guss, 2009, Die Casting – Series production for highly complex thin-walled light metal castings, available on https://www.kug.bdguss.de/giessverfahren-inhalte/druckguss/
Powerguss – Haus der Gießerei-Industrie, Die casting – how does it work?, available on https://www.powerguss.de/was-ist-giessen/druckguss/
Lechuga, G., 2016, Die Casting Facts Infographic, available on https://www.slideshare.net/GermnLechuga/die-casting-facts-infographic
Dynacast, die casting, available on https://www.dynacast.de/druckguss